Background
While the desk is nice for getting around locally, it is cumbersome and relatively slow. I wanted to build something with a smaller profile, more nimble, faster and without the handicap of having to wait 4+ hours to recharge every few miles. With that in mind, the obvious project was some kind of gas powered moped. My friend and fellow creator Peter had introduced me to the board track racer in early middle school, where we decided that it was something that we wanted to do once we had built up the skillset. Having built the skillset through the desk go-kart project, the board track racer (often called "board tracker" or just "tracker" for short) was the clear next step. To clarify, while Peter and I work on the same projects, we each build our own versions separate from each other, each with their own subtleties in design unique to our respective styles.
Frame
Like many great projects, this one started with a good deal on craigslist. I paid $25 cash for a beat up beach cruiser. The beach cruiser is the ideal conversion frame for the project, since it has the signature curve in the top tube and a a sweeping down tube that is reminiscent of the old 1910's Indian bikes.
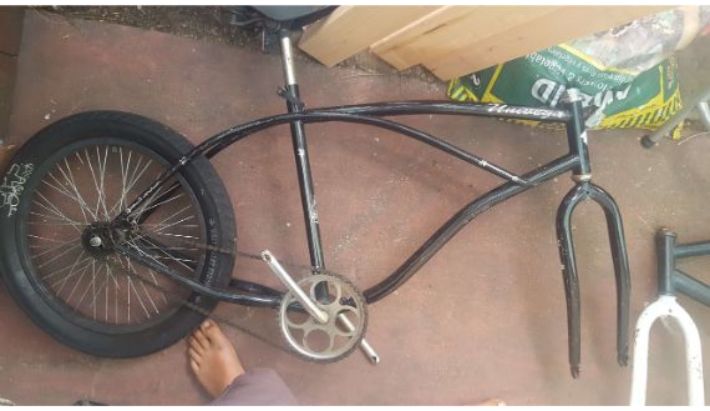
The power plant was another good craigslist find. I got the 3hp Briggs and Stratton horizontal shaft, single cylinder, 4 stroke engine from a guy on craigslist in running condition for $30.
The first task in this build was to build the frame, and the first step in that process was to lay out how I wanted it to look.
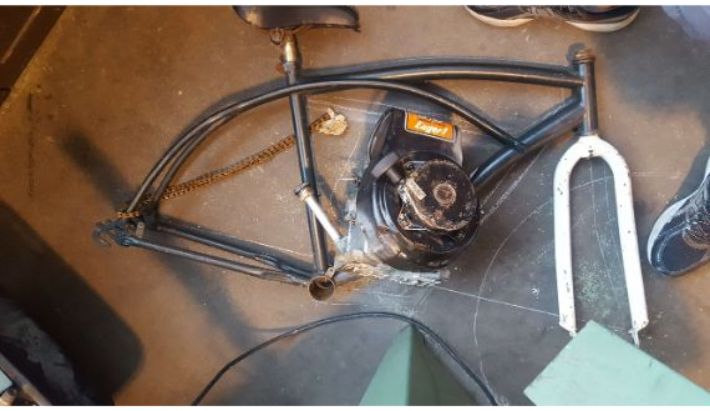
From that picture, its was clear that I would need to replace the down tube in order to accomodate the engine. So, I set to work getting rid of the down tube with a hacksaw and an angle grinder.
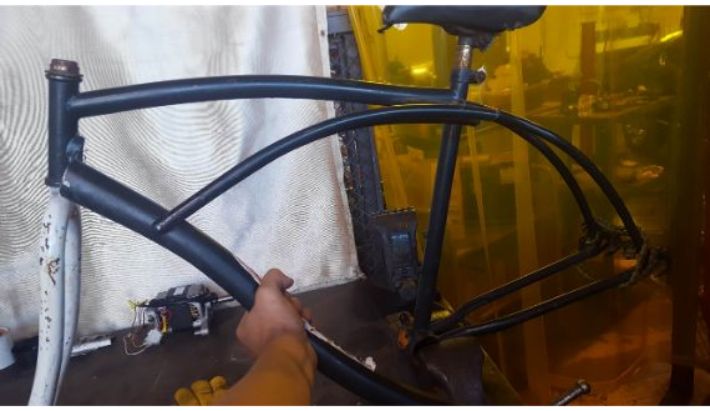
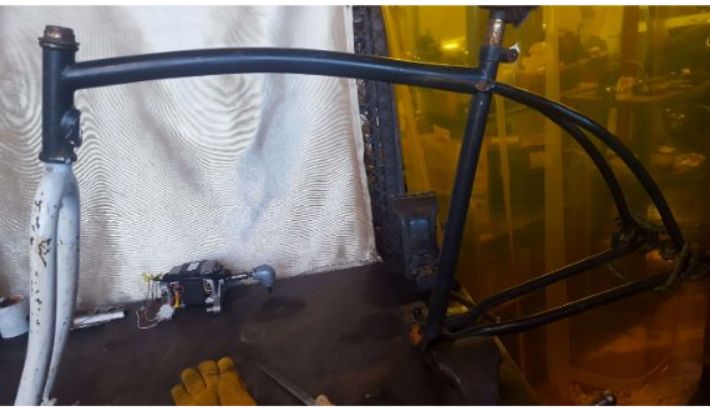
Next, I upgraded the fork. Part of the classic vintage board tracker look is the springer fork. I found one on Amazon and got it.
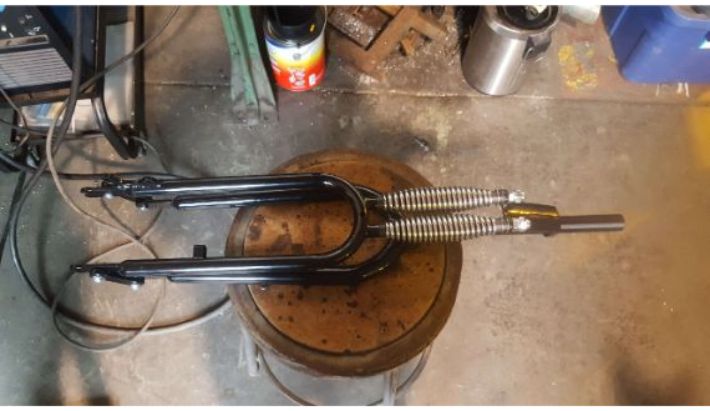
To make the fork fit on the headtube like I wanted, I had to turn some aluminum spacers. I made two, one with decorative grooves, one without.
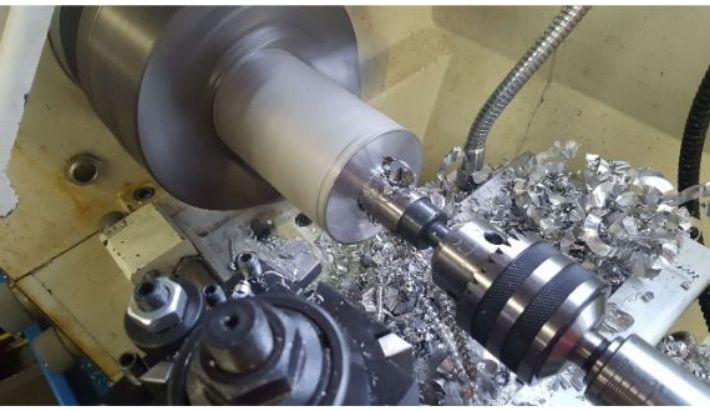
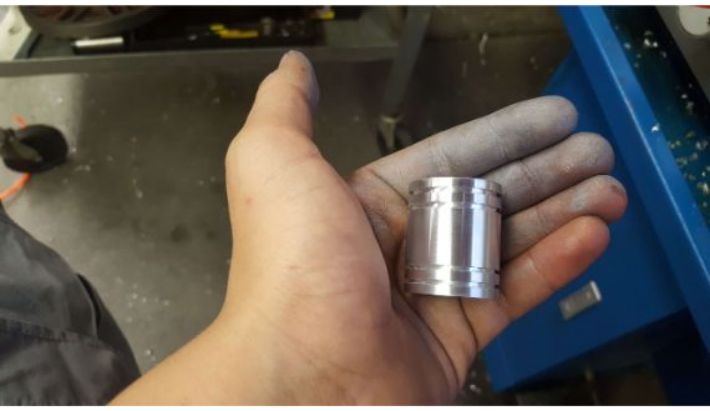
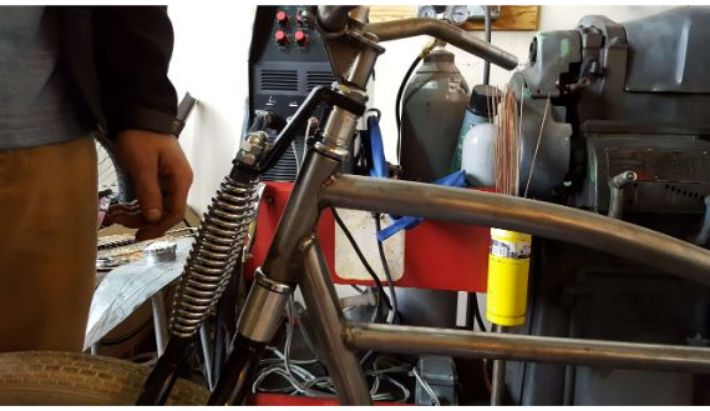
Despite the spacer, I was still left with an absurd amount of threaded mount off of the fork. That had to go.
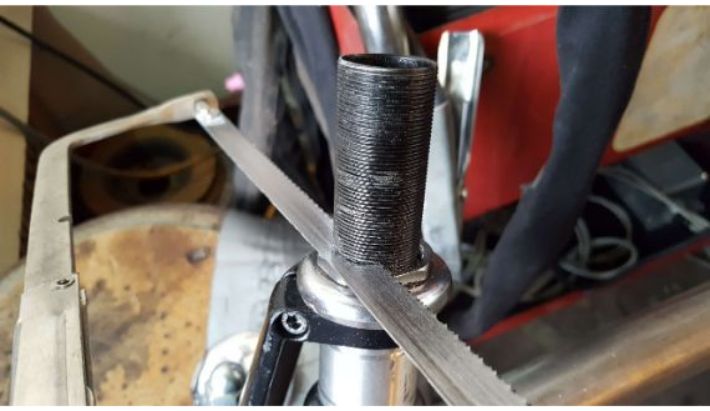
I then bought some really nice cream bike tires, and fitted them to 26 inch mountain bike rims. I also bought and installed disc brakes on the front tire.
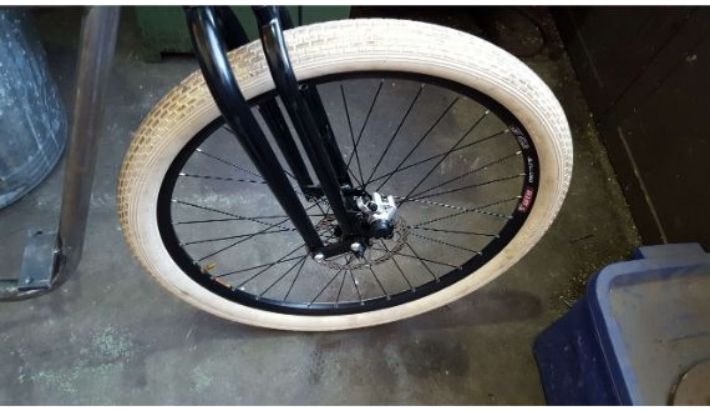
Then, I had to figure out what my replacement down tube would look like. I used Snapchat for this. Snapchat is a great tool because it allows for easy photo editing. I simply took a picture of my board tracker in Snapchat, and then drew in down tubes and cross tubes until I was satisfied.
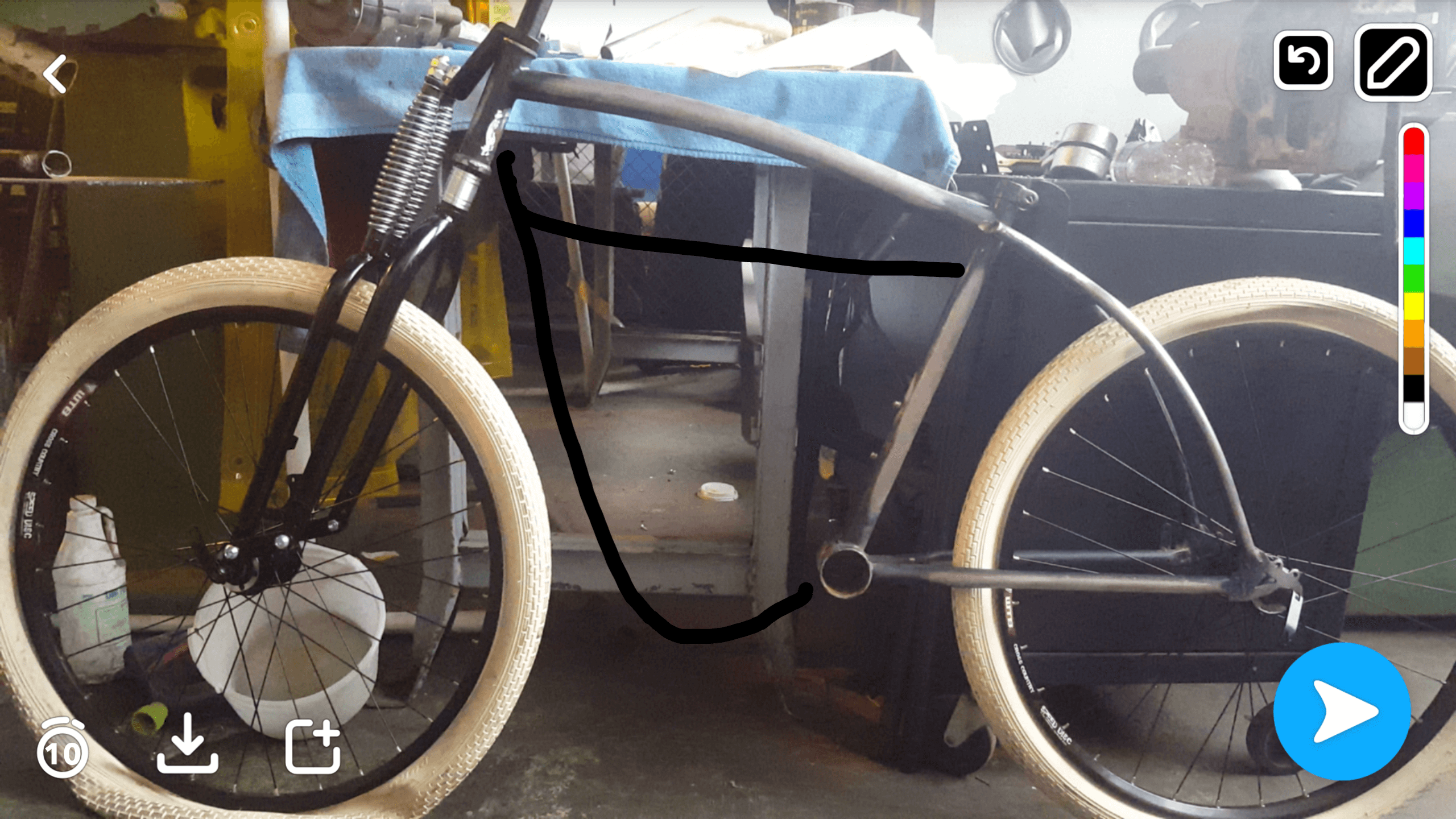
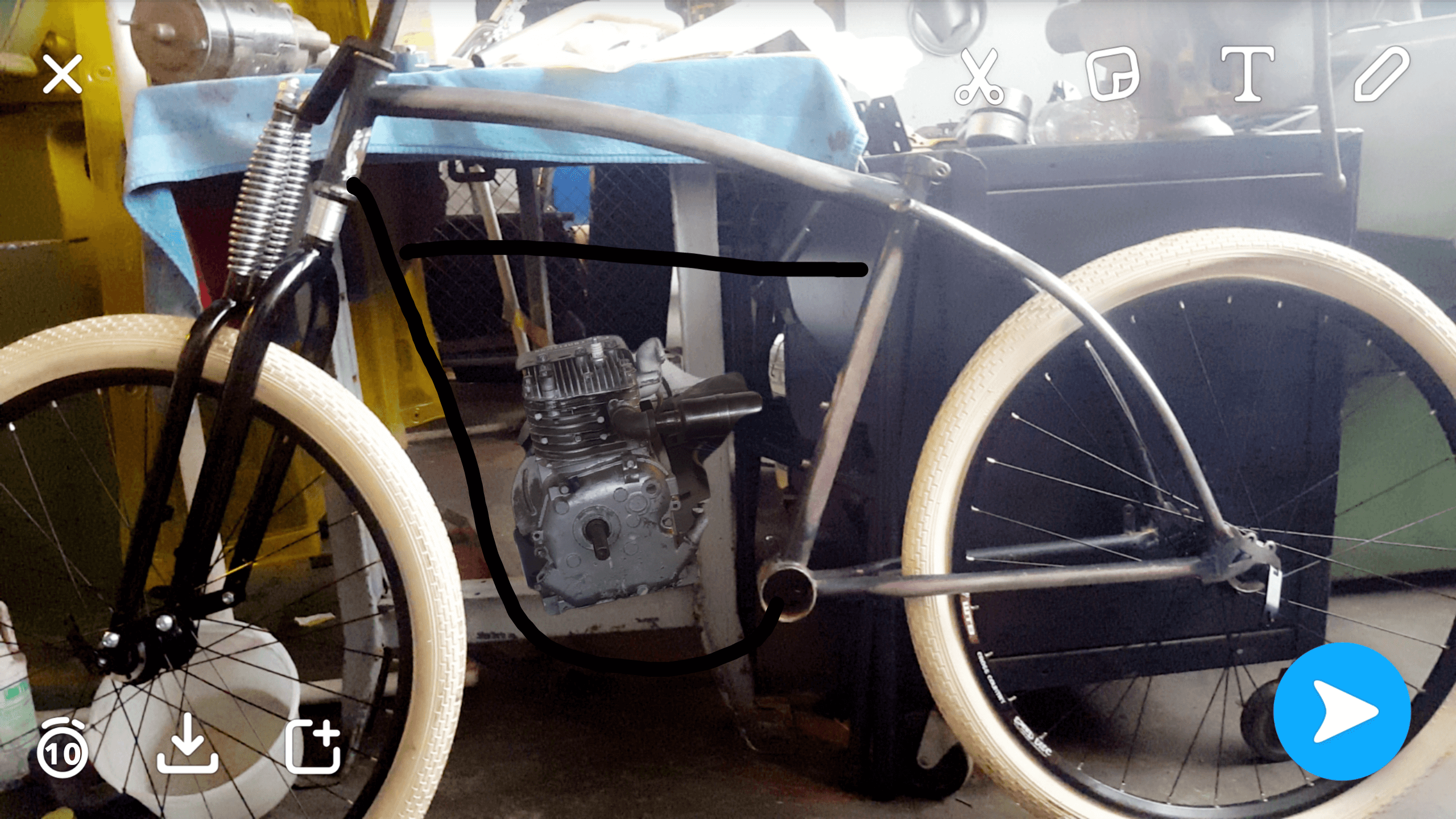
As you can see in the Snapchat screenshots, I wanted to have a down tube with a significant bend towards the bottom. I calculated the angle between the head tube and down tube from the Snapchat image and cut the corresponding angle into a length of 1.25 inch steel round tube, 0.125 inch wall thickness.
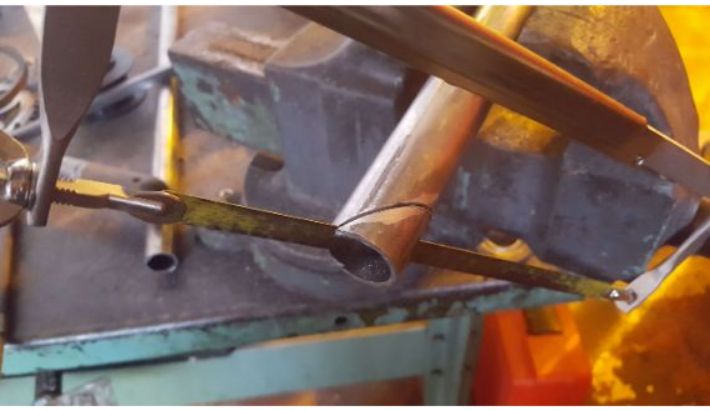
For a better fit up, I ground in notching to the just-cut face of the tube on the bench grinder.
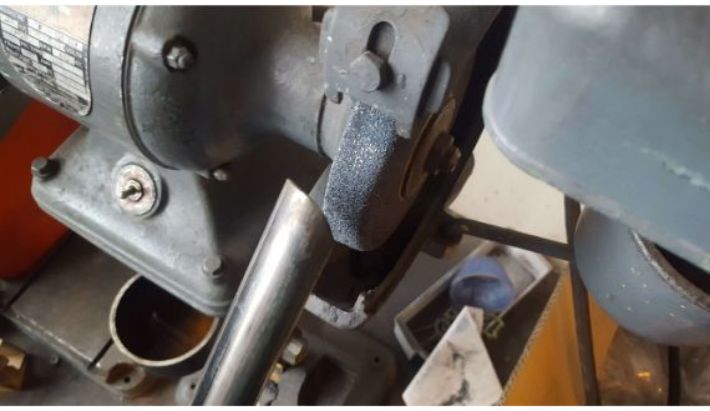
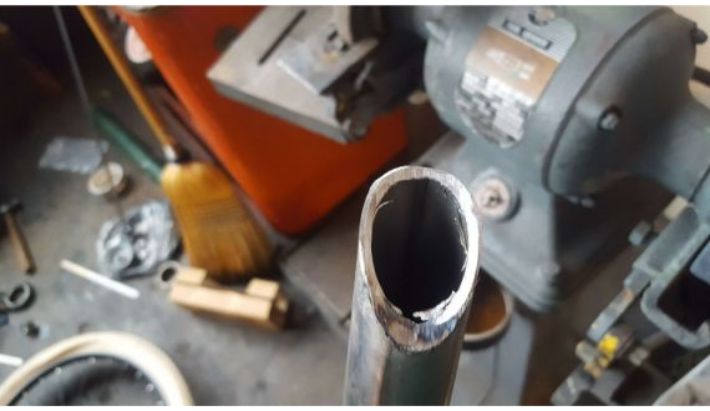
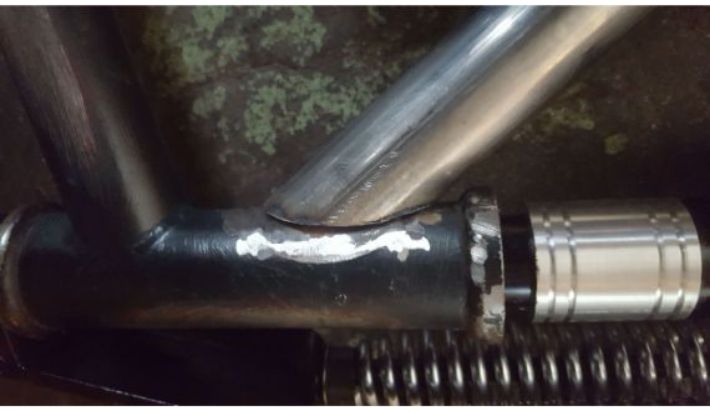
To get the bend, I heated up the tube with an oxy-acetylene torch and wrapped it around a large piece of 7 inch diameter steel round stock.
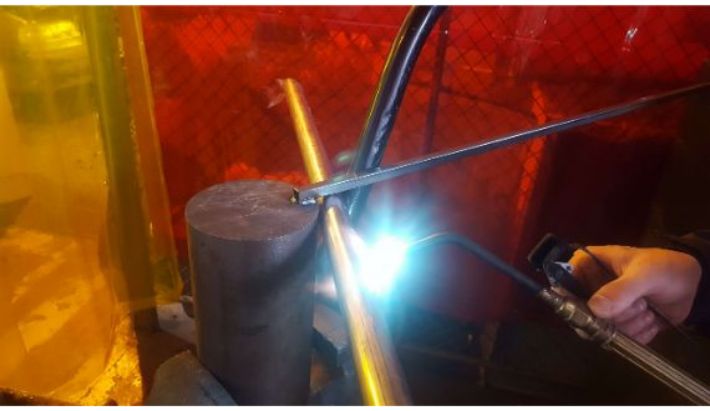
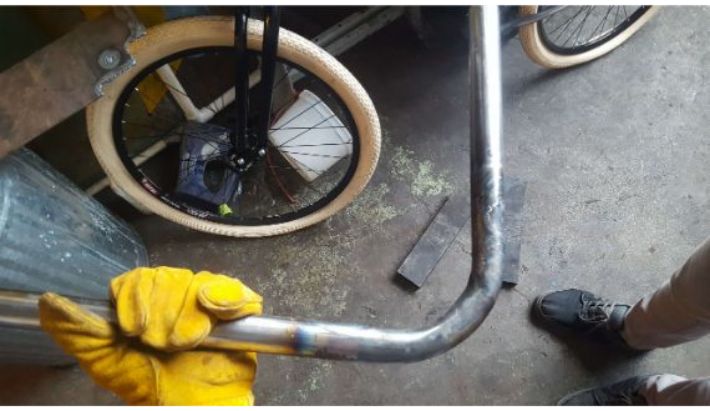
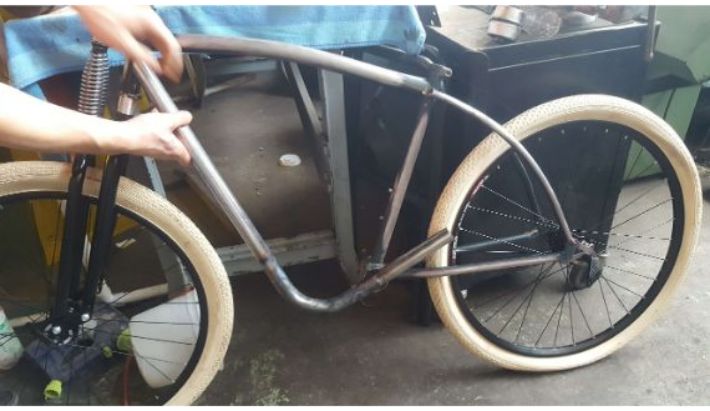
With the bend in, I could then mark the uncut end of the tube for cutting, and then cut and grind in the profile of the attachment point. The lower attachment point is the old bottom bracket shell.
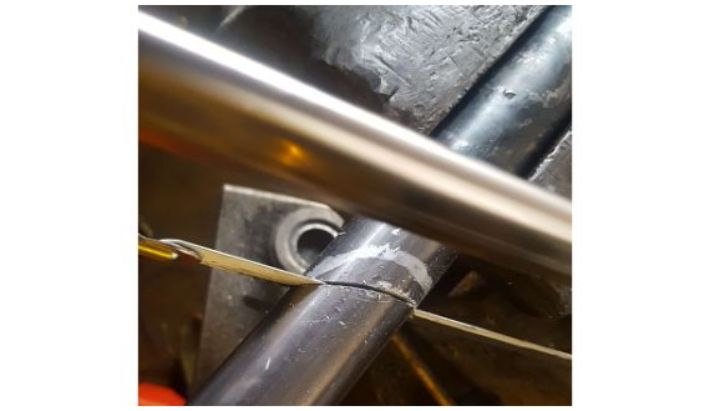
I then welded in the new down tube.
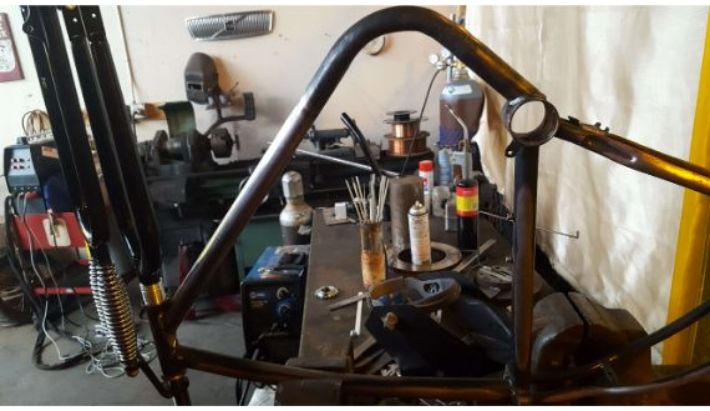
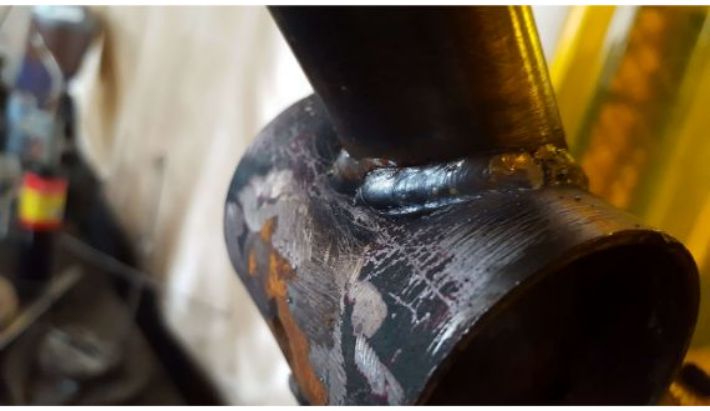
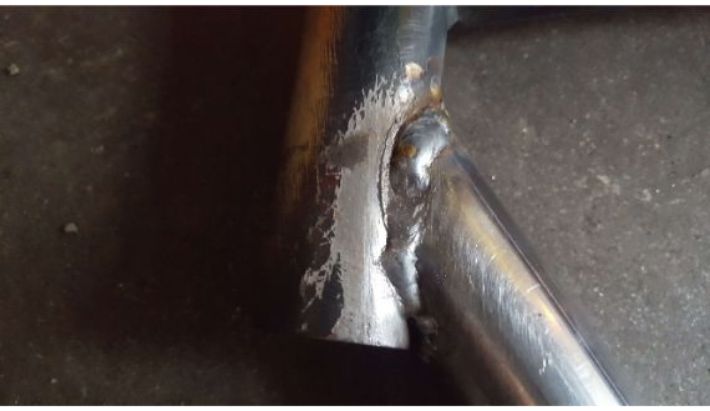
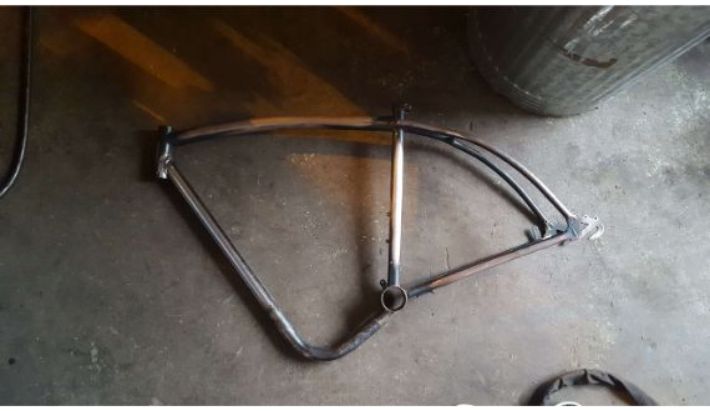
Next, I had to figure out a way to hold the engine to the frame. I decided to fabricate a couple of large pieces of 0.25 inch thick by 2 inch wide steel flat bar to serve as weld in mounts. I drilled holes in them that matched the bolt pattern on the engine, and once the engine had been positioned where I wanted it to be, I welded them to the frame. One mount was welded right atop the bottom bracket shell, and the other was welded to the downtube.
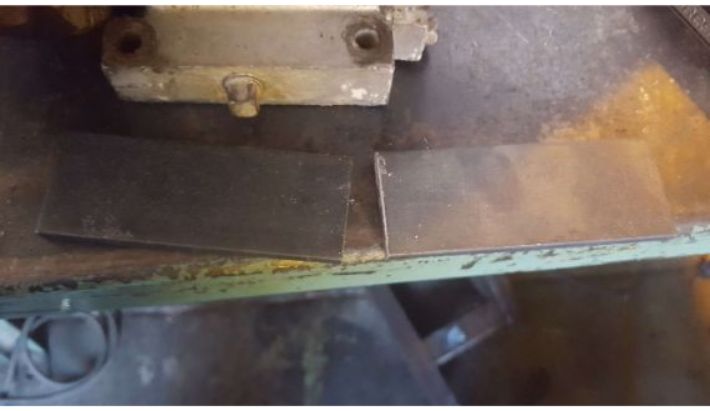
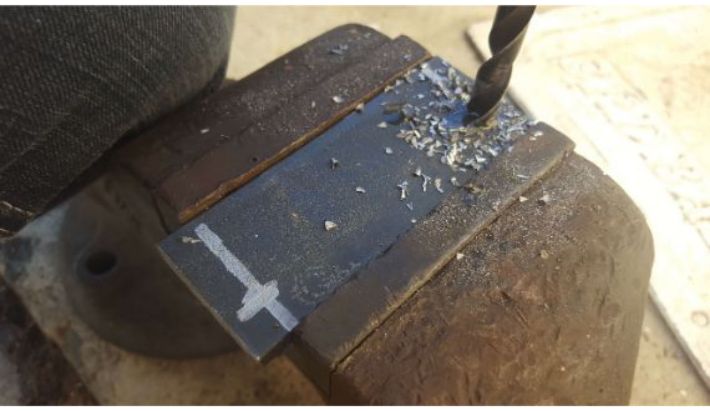
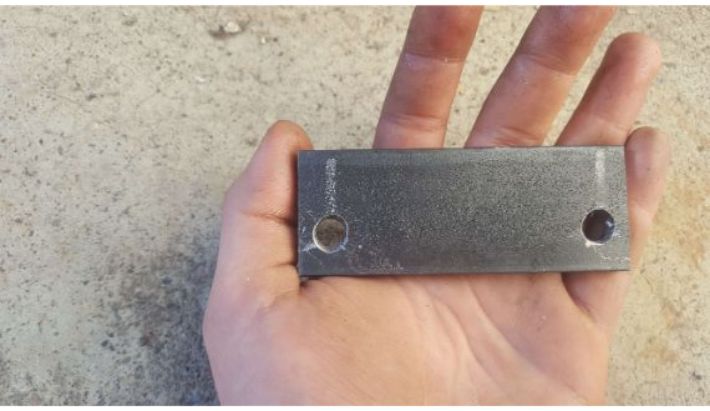
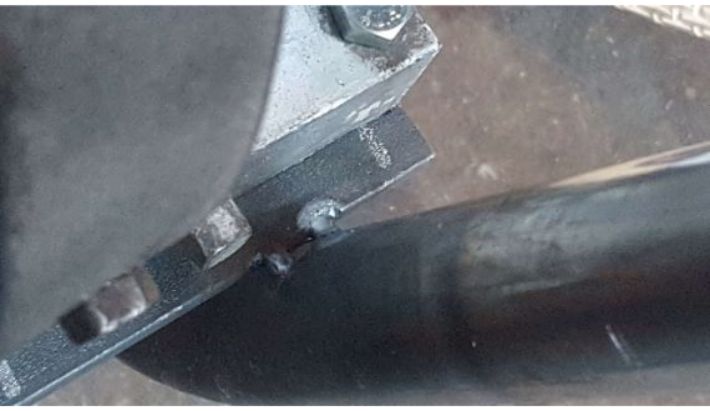
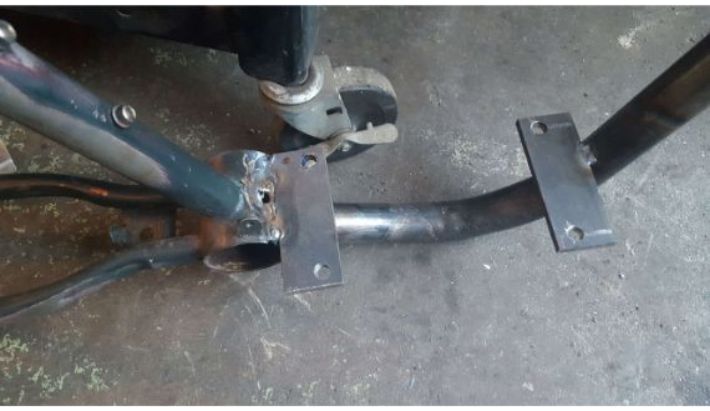
Next, I had to fabricate and install the cross tube. I cut angles into a piece of 1 inch steel round tube, 0.0625 inch wall thickness that matched the profile of the seat tube and the down tube. Then, all I had to do was weld it in.
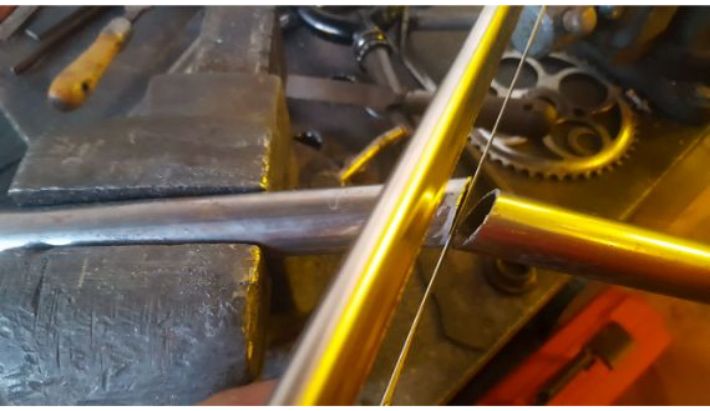
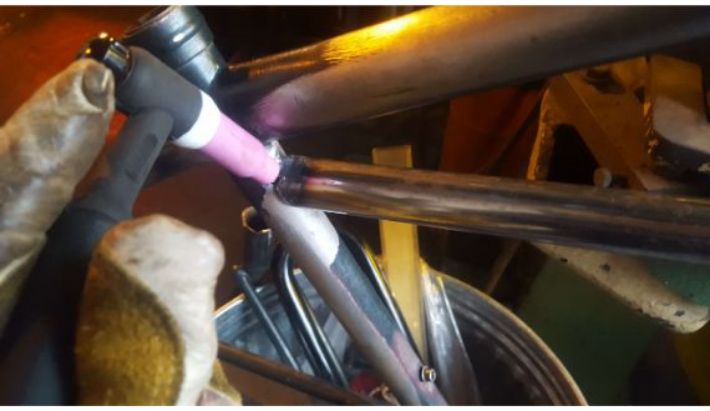
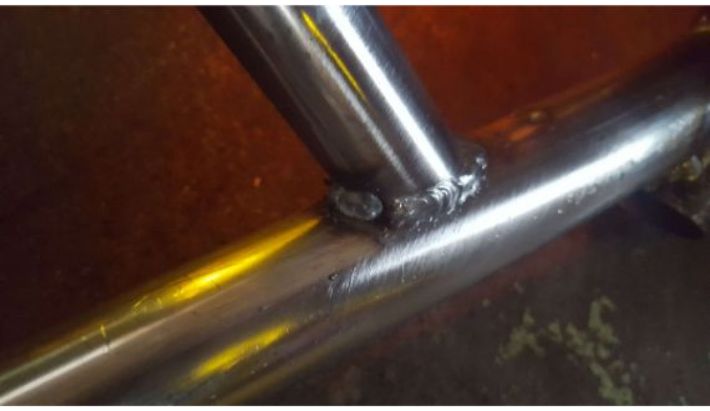
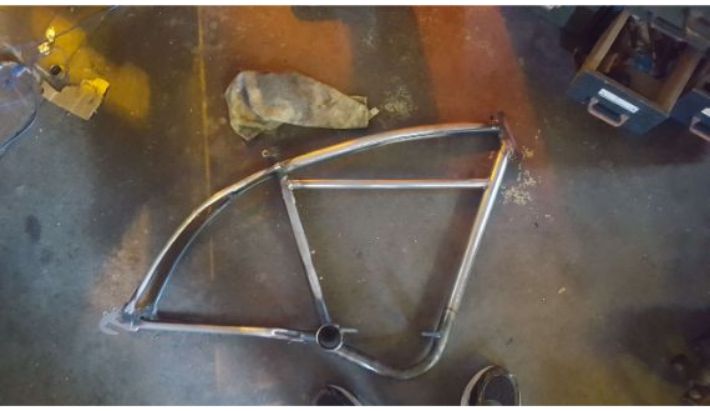
Here the build has reached a critical point- the determination of the drive gear ratios. This ratio would determine much of the following fabrication, as the rest of the bike would need to be built around the transmission. After much thought, I decided to use a gokart torque converter to serve as an automatic transmission. Assuming 3600 rpm from the engine, and a 1 to 1 ratio to the output shaft on the torque converter at full throttle, I needed to seriously reduce the rpm in order to get a reasonable top speed and decent torque. To avoid using an enormous drive sprocket, I then decided to install a jackshaft to allow an intermediate reduction.
I designed the jackshaft to be a 0.75 inch diameter piece of steel round stock, and I decided it would ride in two flange bearings, which would be mounted to the back of the seat tube
To mount the flange bearings, I cut and ground some brackets from the same stock that I used for the engine mounts, drilled holes in them to match the bolt pattern of the flange bearings, and welded them to the seat tube.
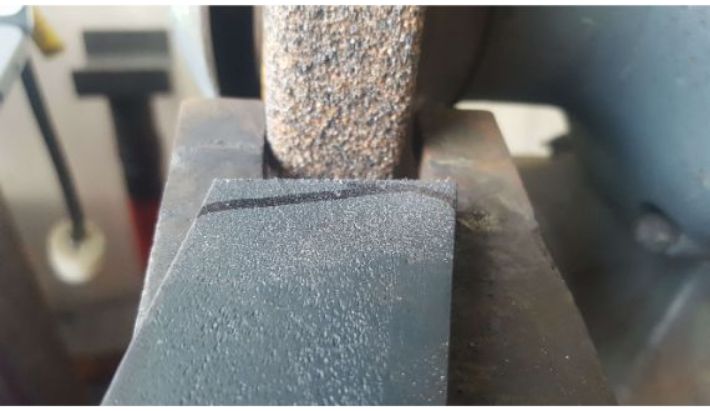
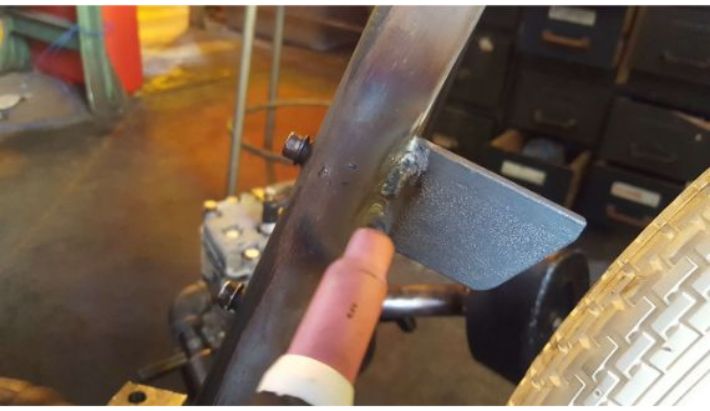
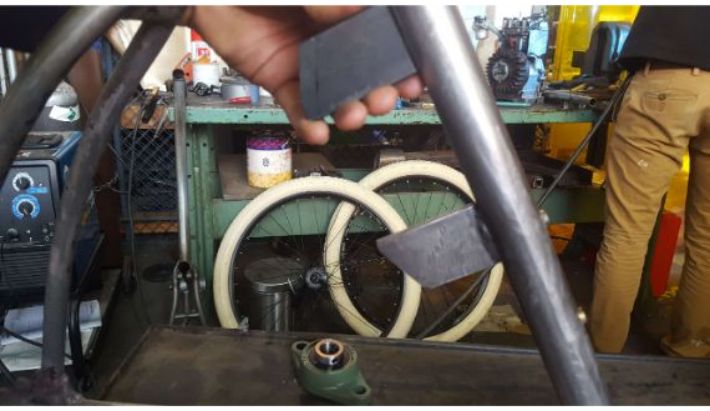
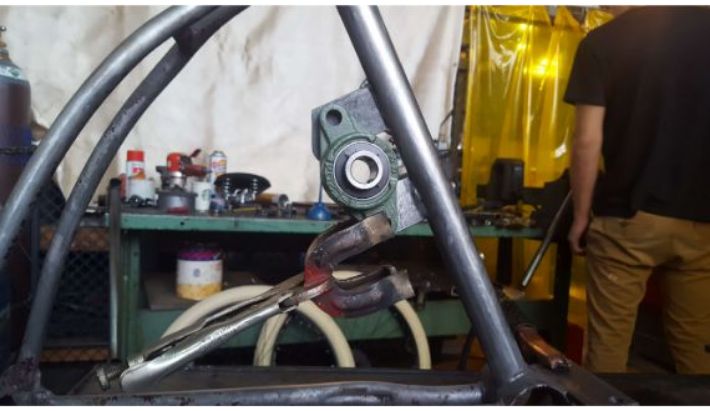
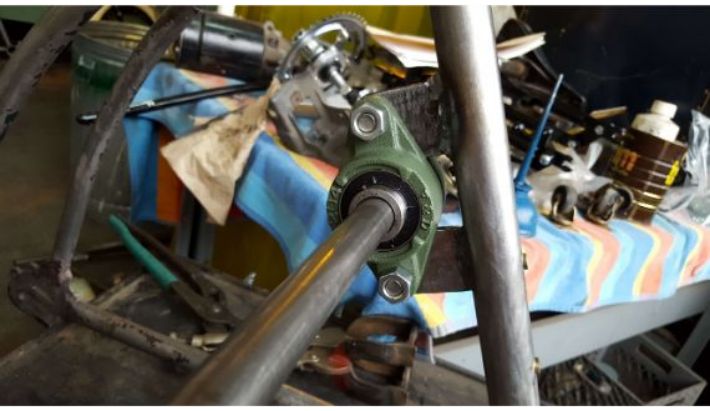
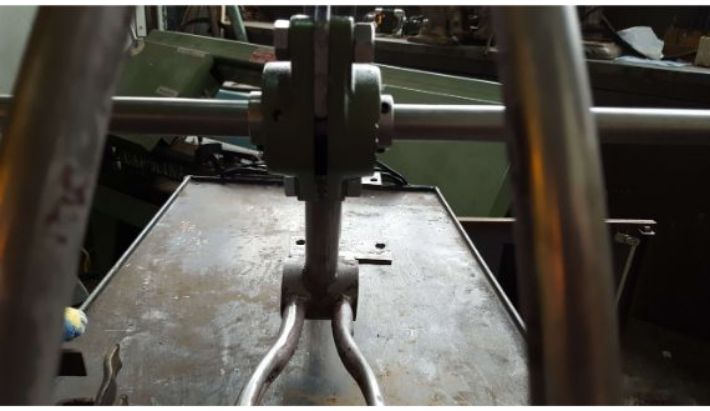
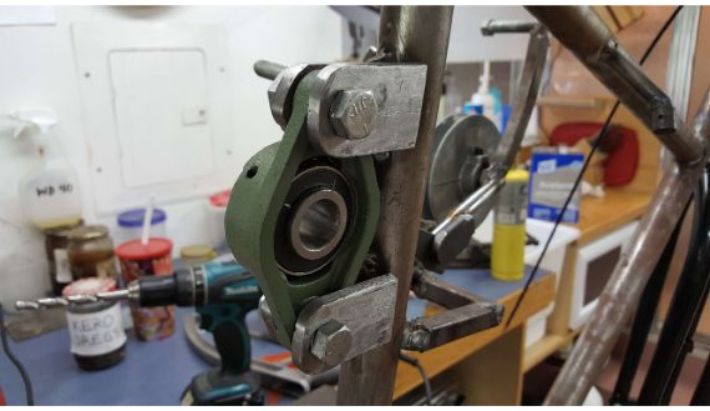
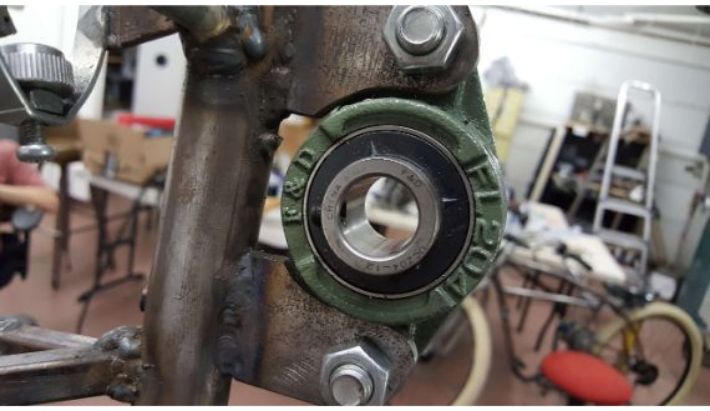
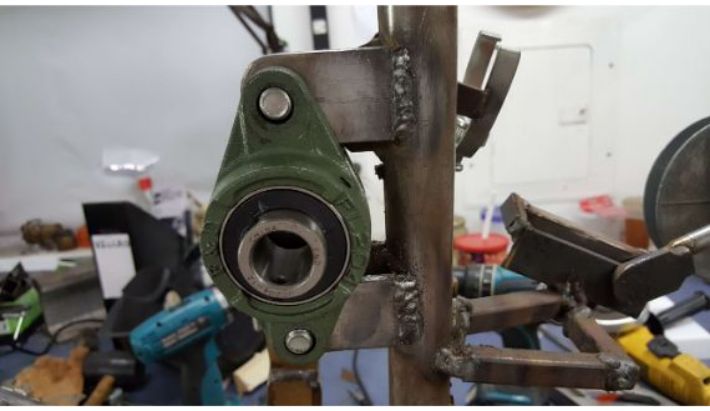
To finish the frame, I just needed to grind out spots in the chain stays and seat stays for chain clearance.
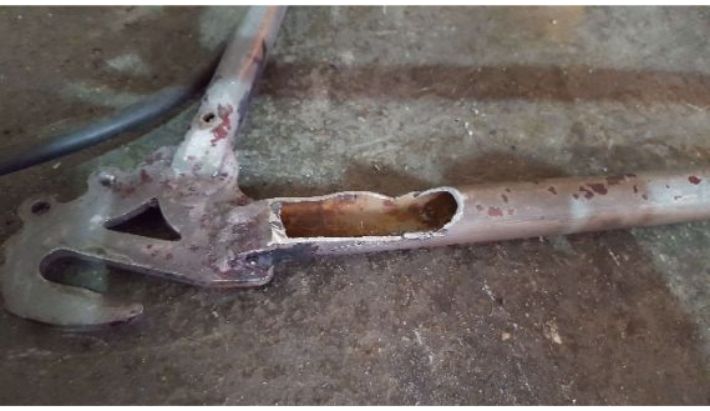
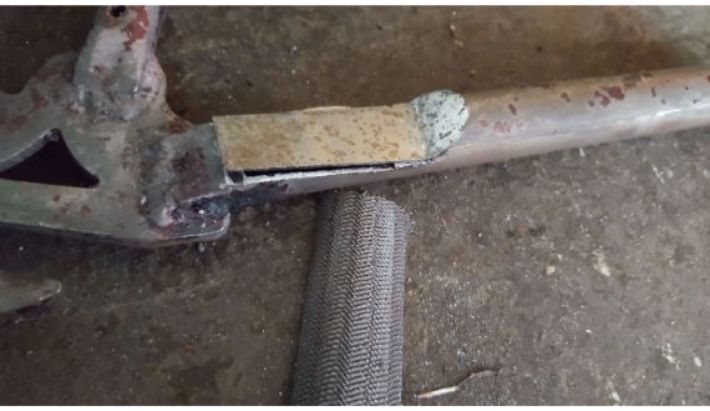
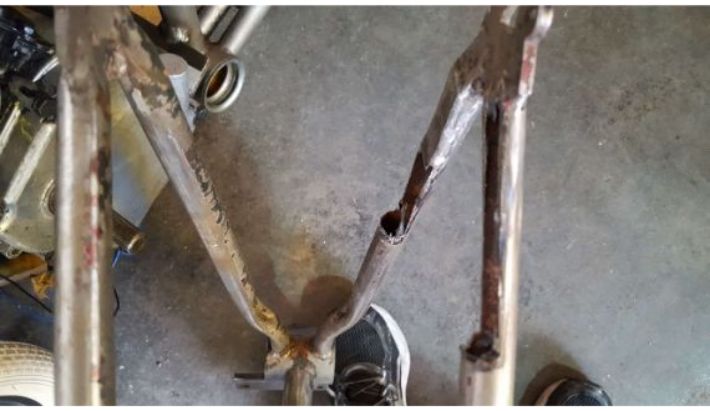
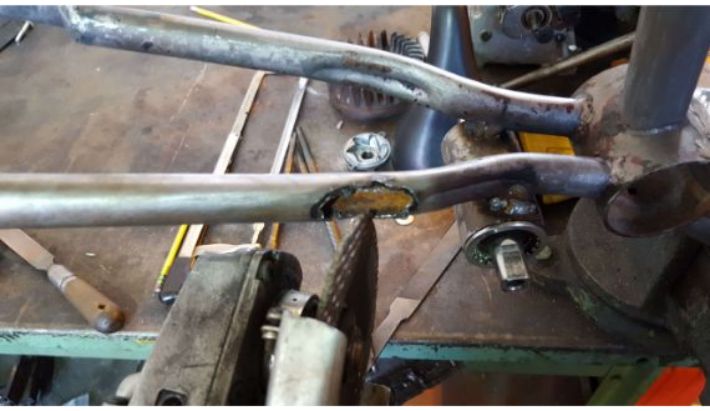
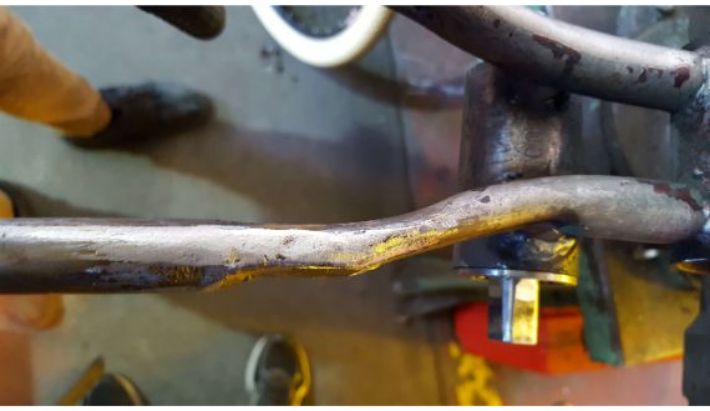
Gas Tank
The next big fabrication event was the gas tank. This was a very tricky thing to fabricate. The easy way to do it would have been to weld a box out of steel, but I knew I wouldn't be able to live with myself if I did that. Go big or go home, I thought. So I went big.
One of my favorite aesthetic parts of the iconic Indian board tracker is the teardrop gas tank, with the organic curves. I knew I had to replicate that. I formulated a basic plan: I would cut some steel shapes, weld them square, and to get them to curve organically, I would force pressurized water into the tank to blow it up like a balloon.
To get the steel panels, I started by making a styrofoam model of the tank. I made it by spray-gluing a bunch of sheets together into a block, then drawing the profiles of the tank, and then using a hot knife to carve the foam into the final shape.
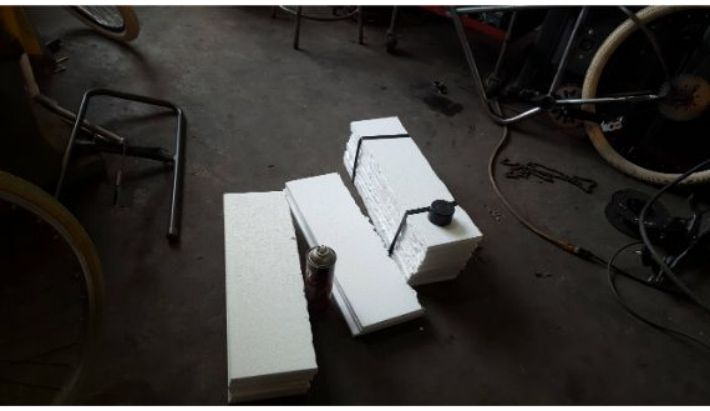
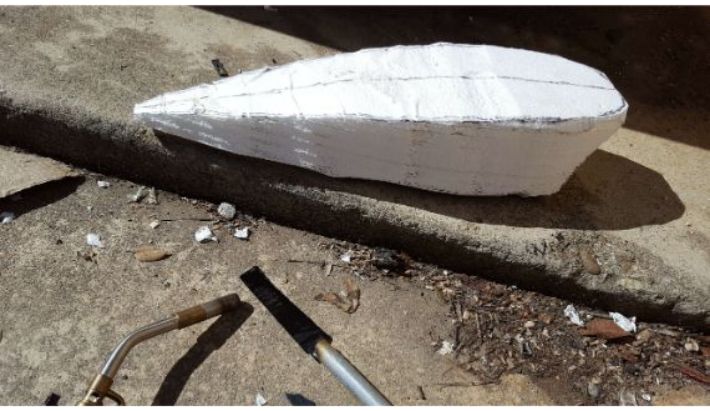
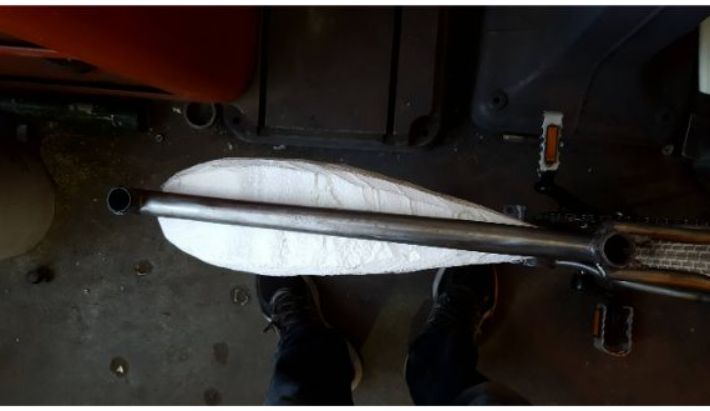
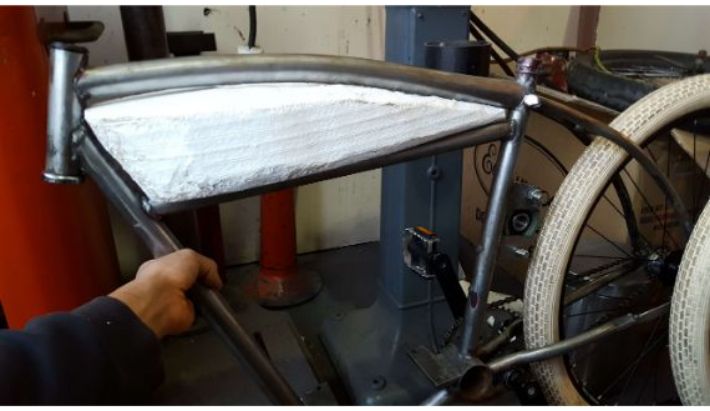
To transfer the 3D model to 2D templates, I covered the whole form in tape, and cut along the tape in places where I thought a seam could reasonably go. I then peeled those templates off of the foam and stuck them to the sheet steel, where I could then trace and plasma cut out the profile.
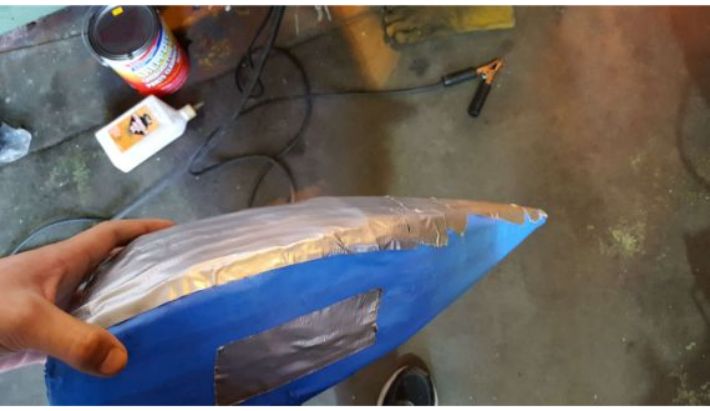
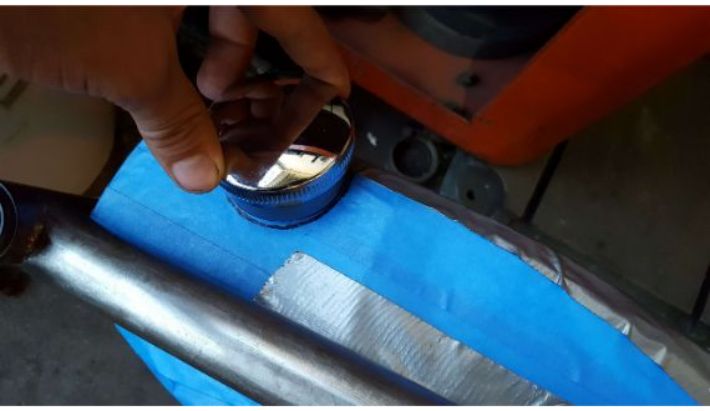
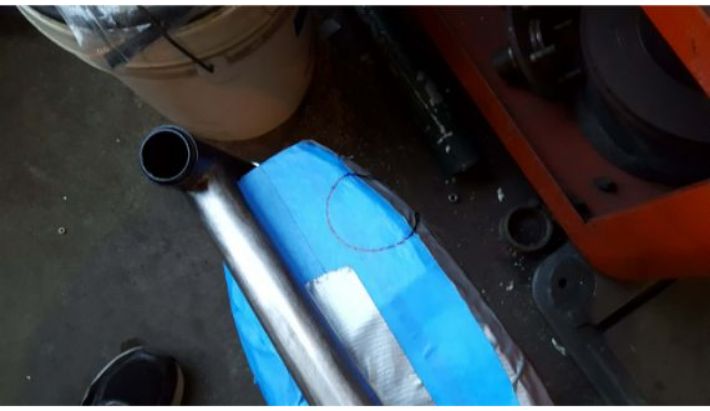
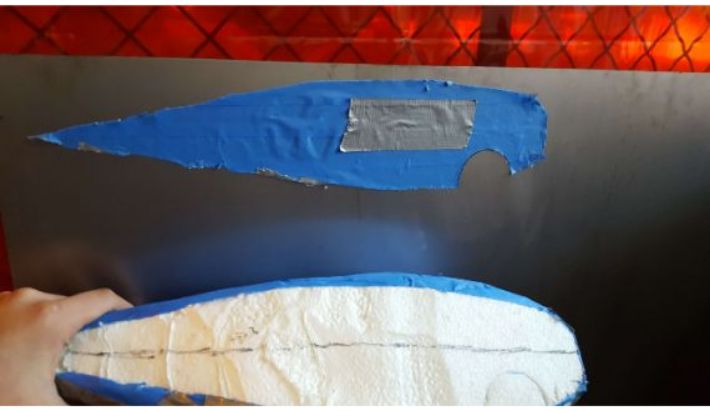
As you can tell, these templates did not hold up well due to the tendency of the masking tape to rip, so I made a new set of templates from duct tape.
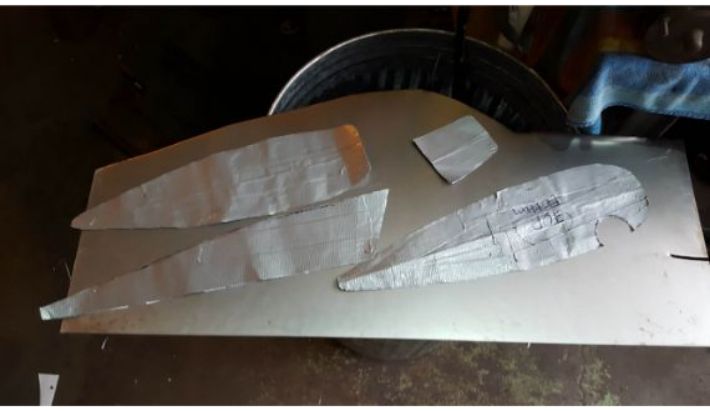
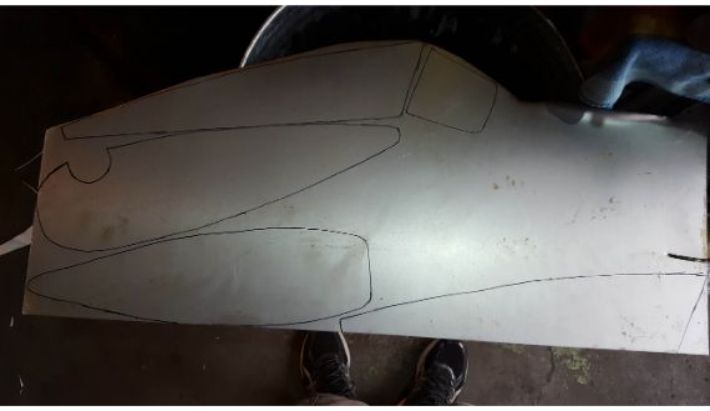
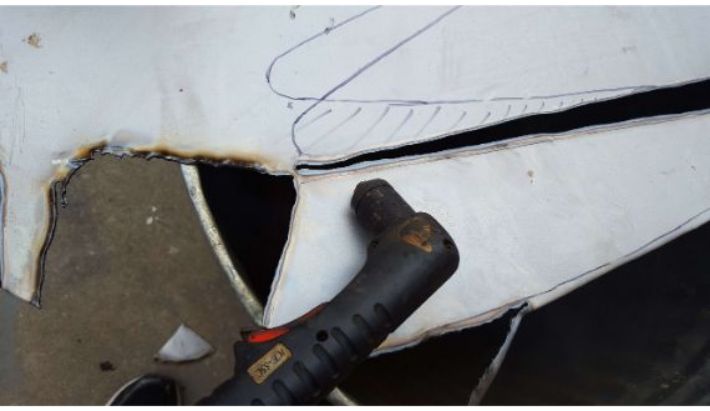
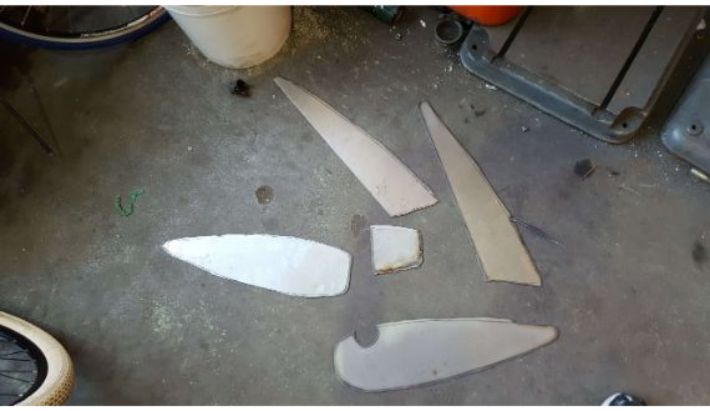
From there, It was just a matter of welding the pieces together and then hydroforming the tank to its final shape.
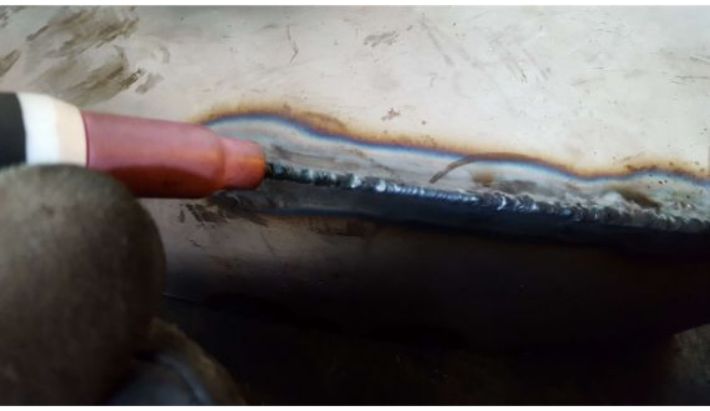
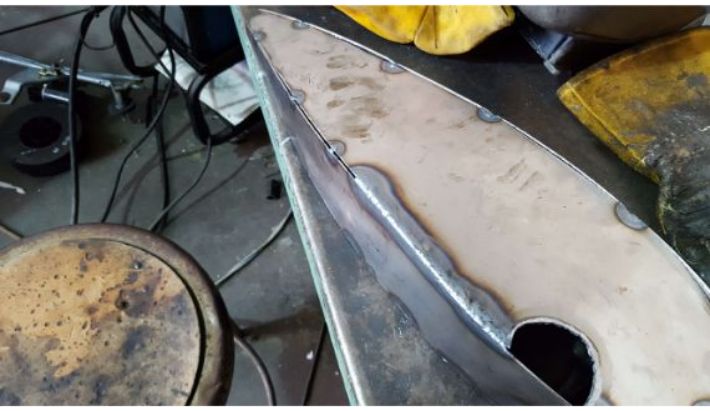
Not pictured, I fabricated an adapter out of steel that attached to a friend's electric pressure washer. I welded the adapter into the vertex of the tank. Shout out to Javid Alasti for letting me potentially ruin his family's pressure washer! After filling the tank to the brim with water (to avoid air pockets that could compress and turn the tank into a bomb), I forced a 120 psi stream of water into the tank, which puffed it out quite nicely.

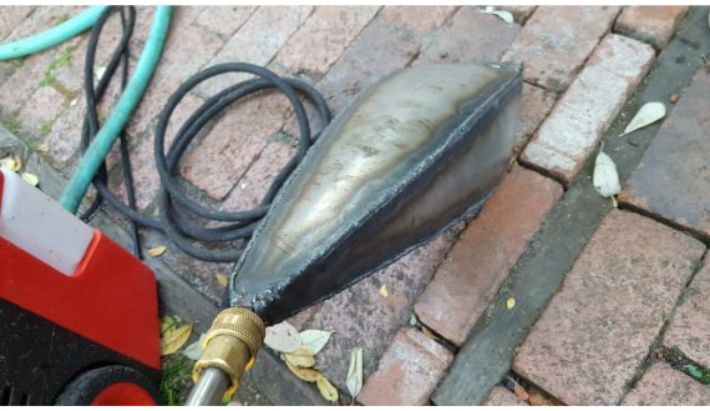
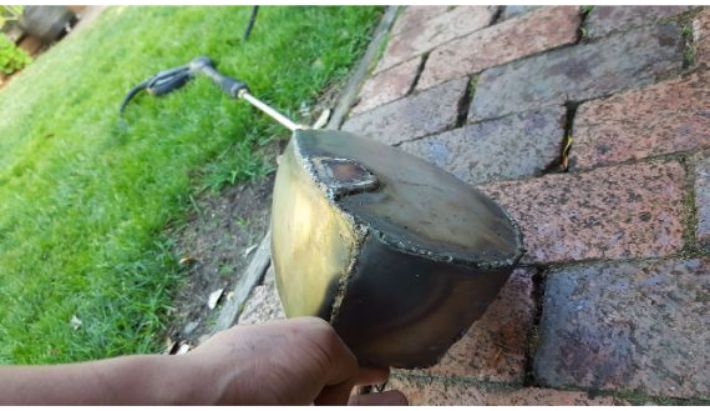
With the hydroforming done, I just had to weld in the bung after cutting out the patch that I had welded on for water proofing. The bung was a weld in kit from eBay that came with a matching cap. I also had to figure out a way to mount the tank to the frame. I decided on fabricating some threaded inserts that I could then weld into the top of the tank, so I could weld corresponding tabs onto the top tube and bolt the tank on through those.
I made the inserts by tapping 1/4-20 thread into some 0.375 inch round steel. I turned a small shoulder to prevent the inserts from falling into their respective holes in the tank, and also to provide some area to weld too.
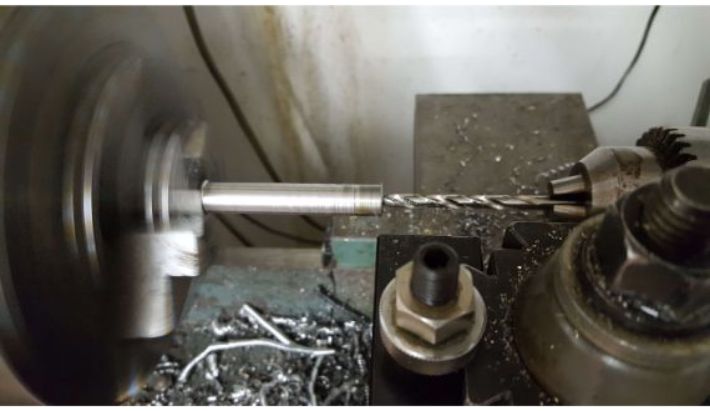
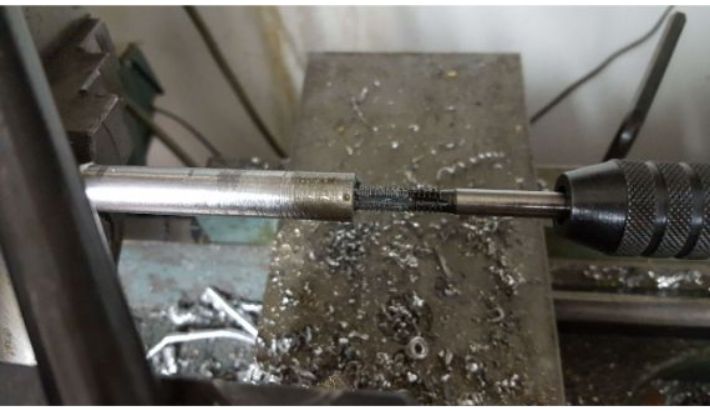
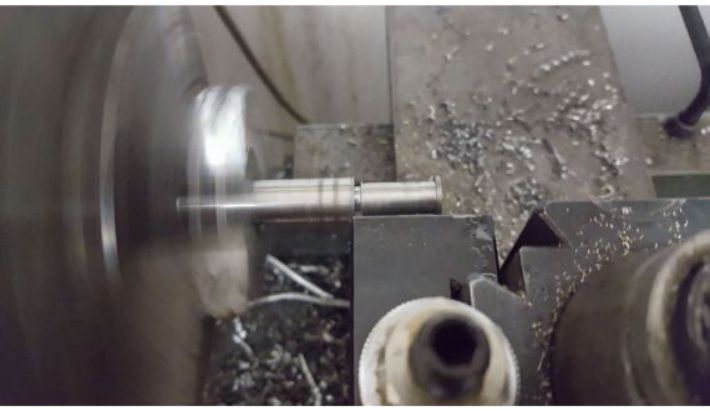
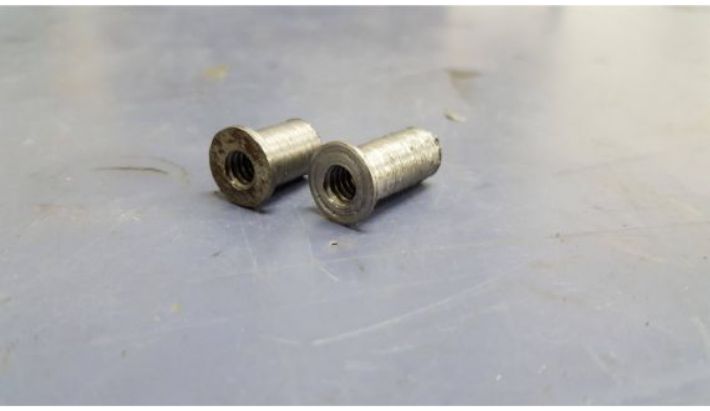
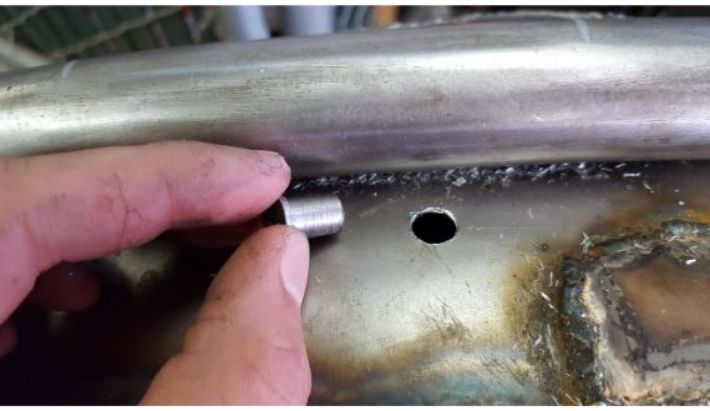
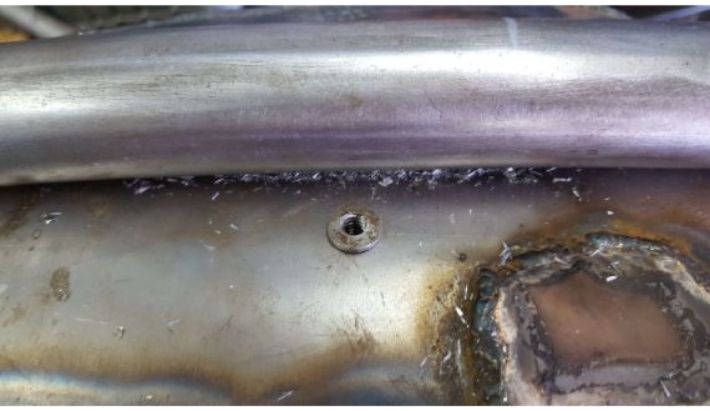
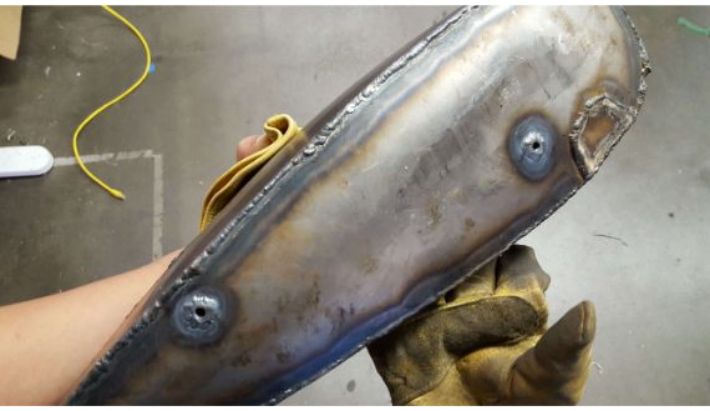
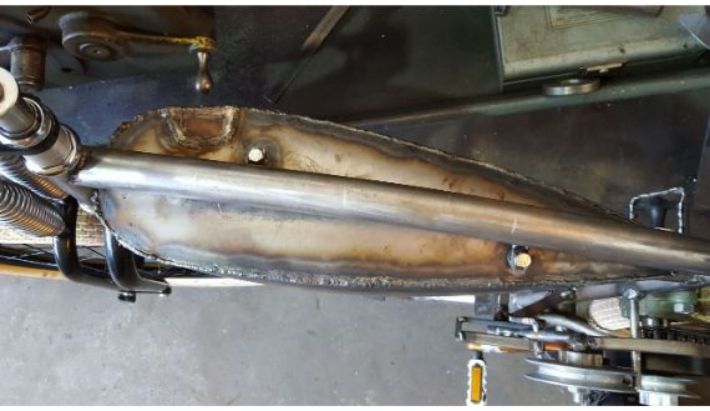
Next, I drilled a hole in the bottom of the tank and silver-brazed in a brass barb fitting to accept flexible fuel lines.
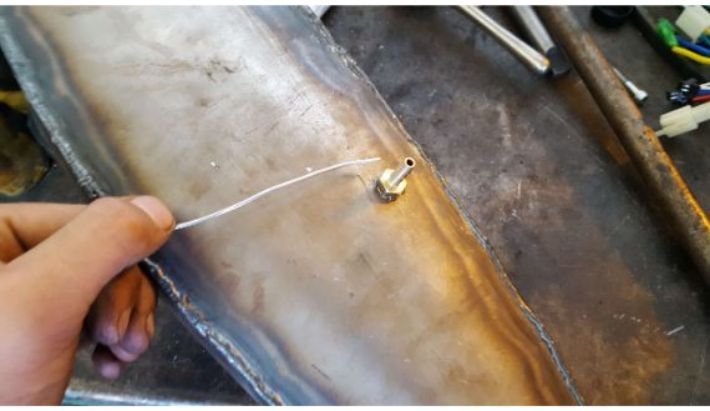
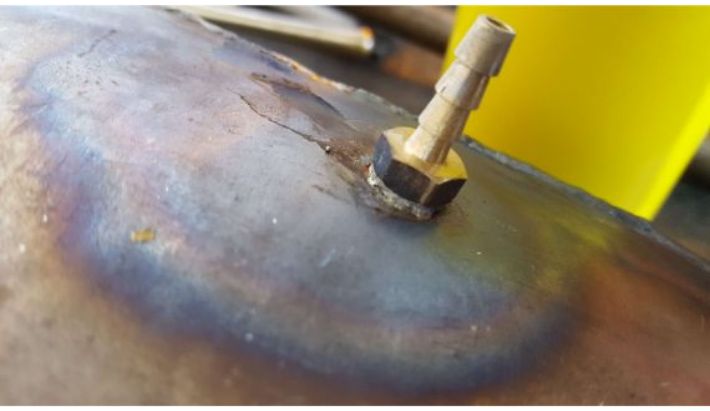
The Seat
Another iconic part of the board track racer is the leather saddle seat. Looking online for one only yielded crappy cardboard knockoffs or $300 art pieces. So, I decided to make my own.
I started the build by fabricating a seat pan out of 0.125 inch thick sheet steel. I drew an outline on the plate, and then cut it out with the plasma cutter. I bent the pan to its final profile by heating it up with the oxy-acetylene torch and then hammering over the same steel form that I used to bend the down tube.
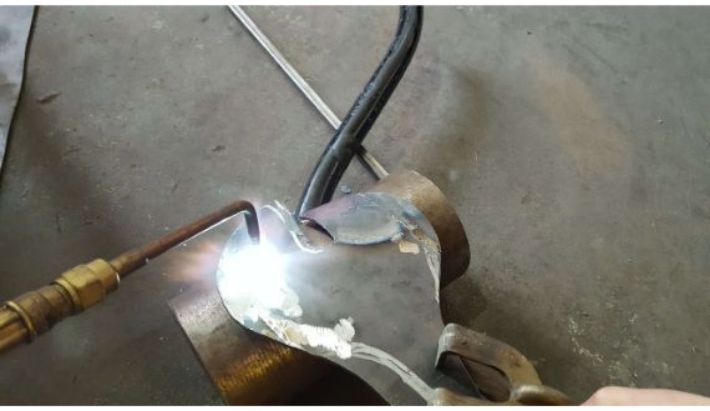
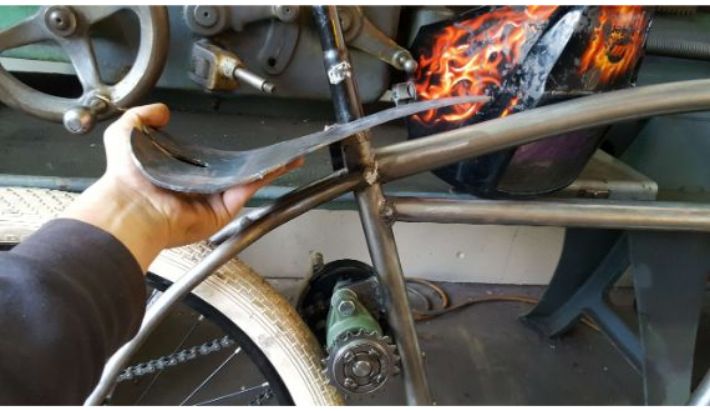
Then, I welded a piece of steel tube to the bottom of the pan to act as a seat post.
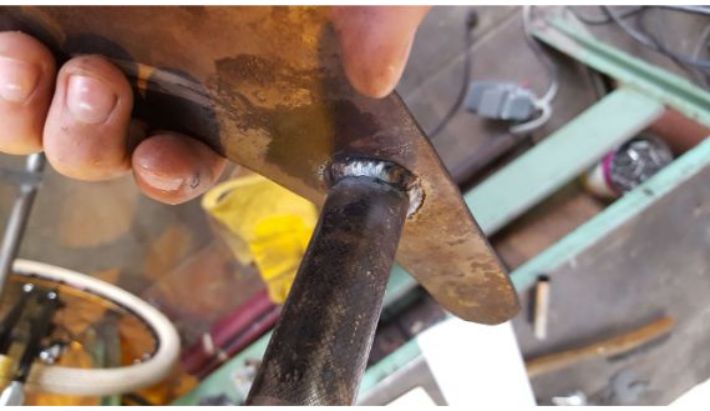
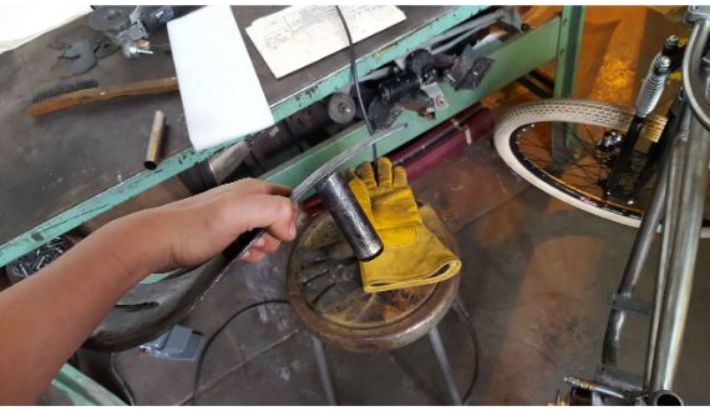
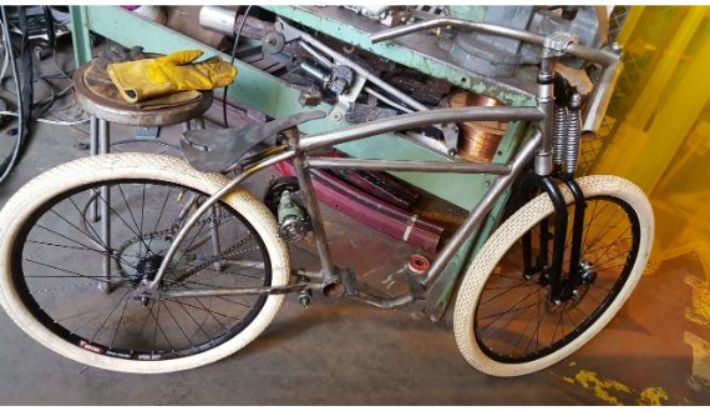
As you can tell from the picture above, the seat pan is only supported by the seat post at the very front, and would likely bend if sat on. To prevent this, I needed to weld up a rear support. I fabricated the support out of three sections of 0.5 inch square tubing welded into a triangle shape to meet the cross support at the top of the chain stays.
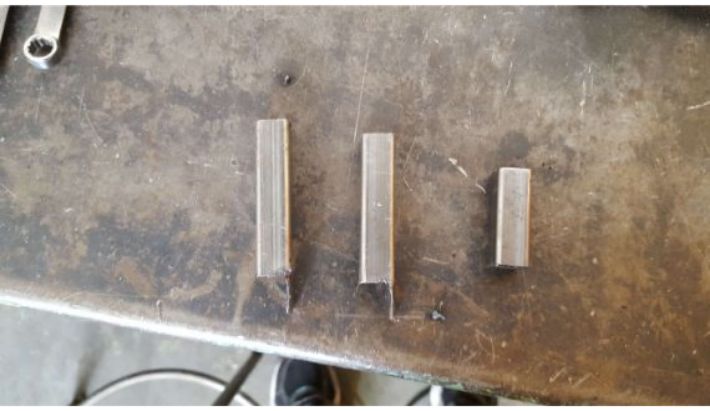
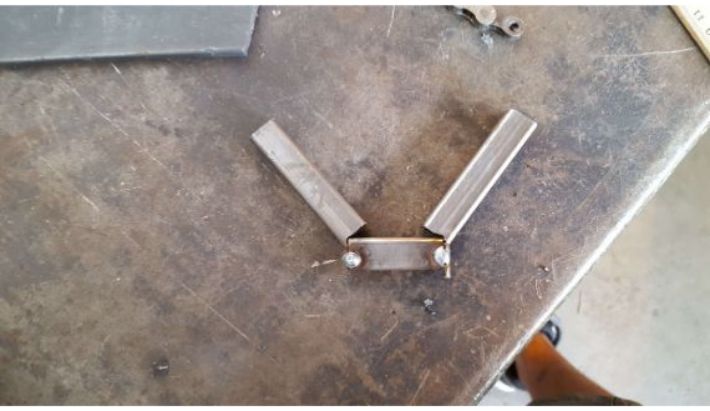
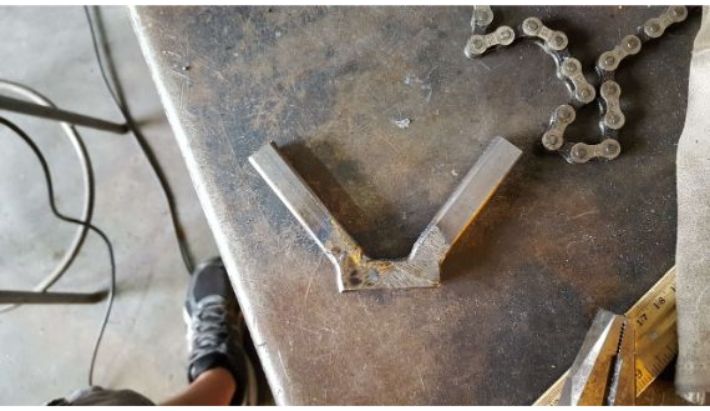
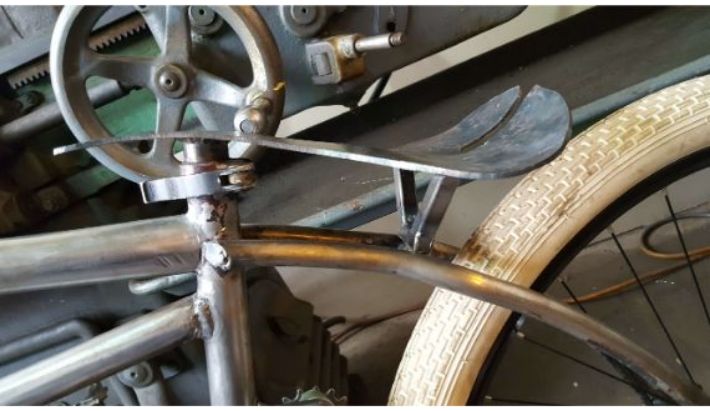
For the cushioning, I used closed cell foam from an old package, which was about 1 inch in thickness. I used household goop to stick the foam to the pan, before shaping the foam with a hot knife to the final profile.
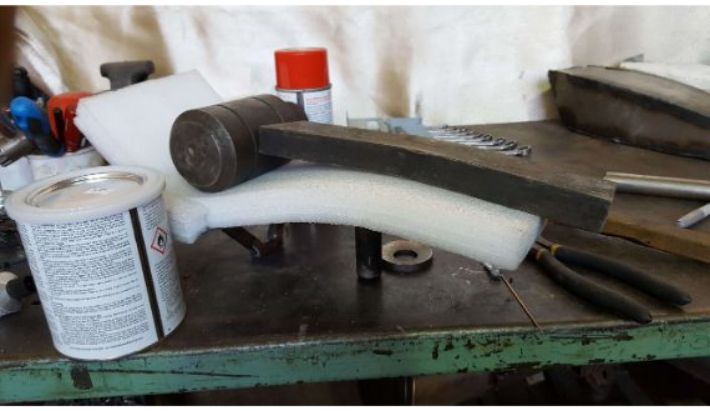
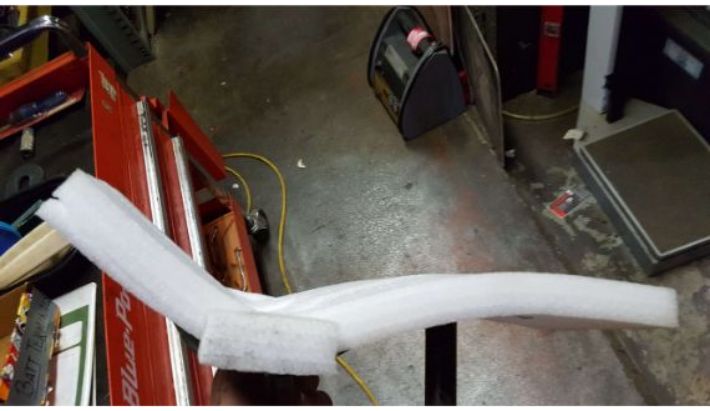
The next part was adding the leather. I found a buck skin on eBay for $35 and pulled the trigger on it. When the skin arrived, I cut out two oversized profiles out of the hide, and used household goop to stick one to the underside of the pan. Following that, I trimmed the edges of that profile to protrude off the pan by 0.25 inches. Then, I pulled the top profile taut around the foam, and clamped it to the edges of the underside profile using binder clips. I used white tacky glue to stick the edges together. I finished the leather work by using an awl to poke evenly spaced holes all around the edge of the seat before stitching it together with waxed thread. I then trimmed the edges, and the seat was done.
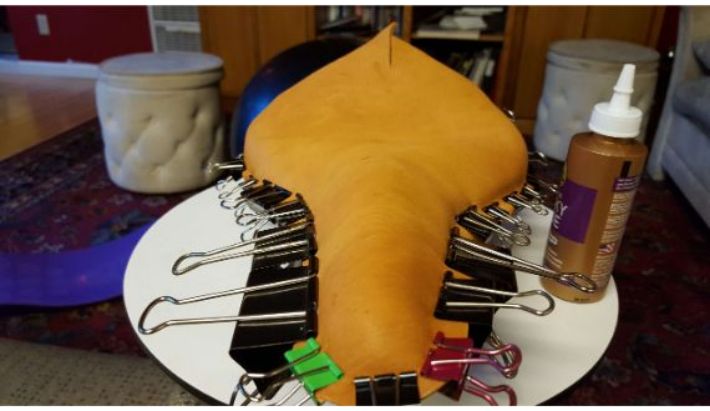
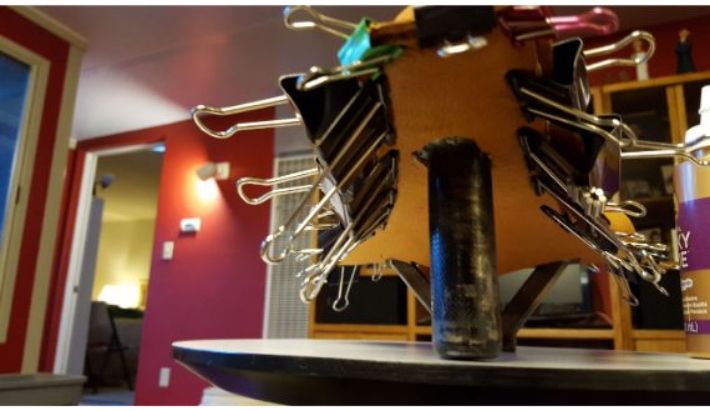
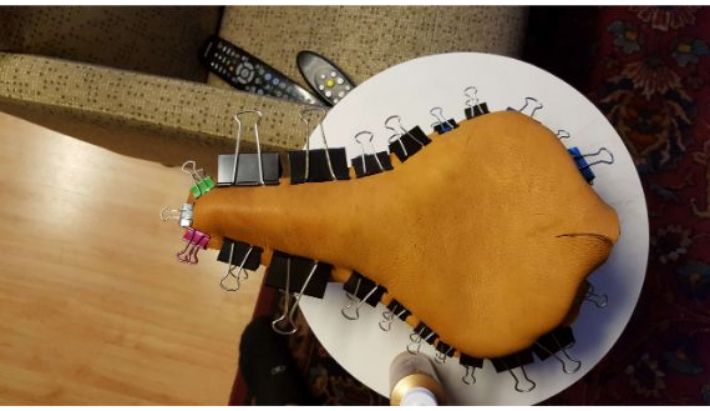
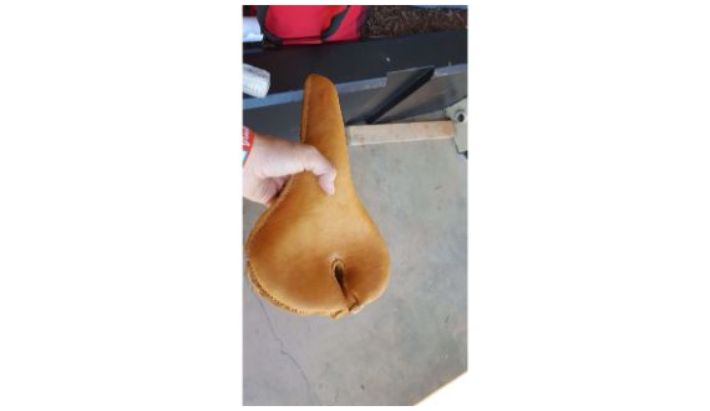
The Throttle
No motorcycle is complete without an internal throttle. Of course, I had to build mine custom. This is one of the more complex mechanisms in the build.
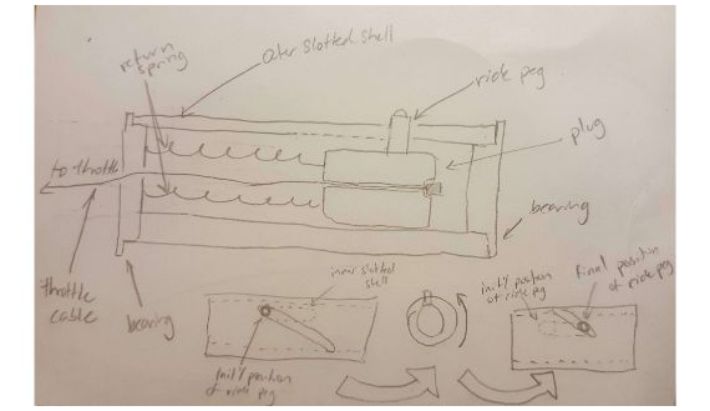
So how does an internal throttle work? Well, as you can see in the picture above, there are three main components: an inner sleeve with a slot cut parallel to its axis, an outer sleeve with a slanted slot cut into it, and a plug with a ride peg that, well, rides in the slots. These pieces are held concentric to each other with bearings. The basic idea is that the plug rides smoothly in the inner sleeve as the ride peg rides the slot. This whole assembly is fixed to the handle bar, and the outer slot shell goes over it, so the ride peg rides both in the straight slot and the slanted slot. When the outer slotted shell is rotated, the slanted slot forces the ride peg to move along the straight inner slot, causing the displacement needed to actuate the throttle on the carburetor.
Fabrication began with the creation of two endcaps for the inner sleeve (a length of 1 inch dia. 0.0625 inch wall thickness steel round tube), which would eventually hold the bearing and mount to the handle bar. Unfortunately, I lost the footage of machining the inner sleeve, which basicaally just consisted of milling the straight lengthwise slot. I turned the endcaps out of 1 inch solid round steel bar, and cut threads into them to accept the handle bar and bearing mounting axles. On the thicker endcap closest to the handlebars, I drilled and tapped some holes to accept eye bolts to hold the return springs.
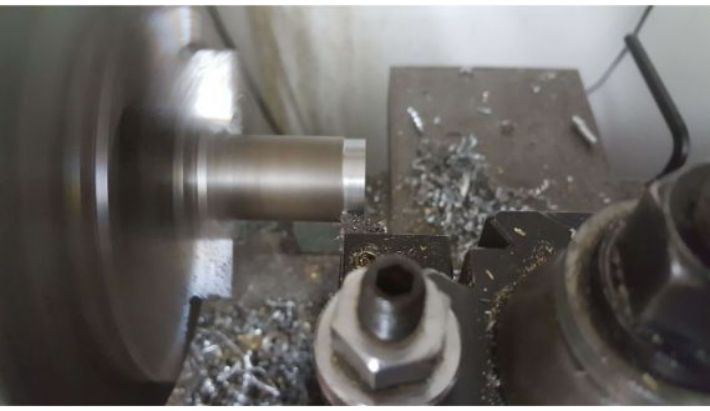
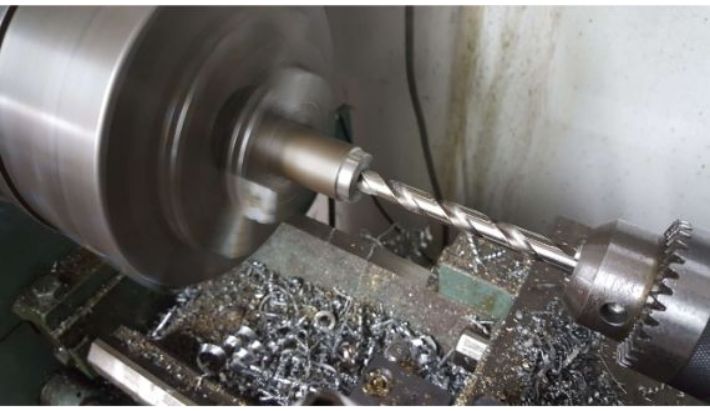
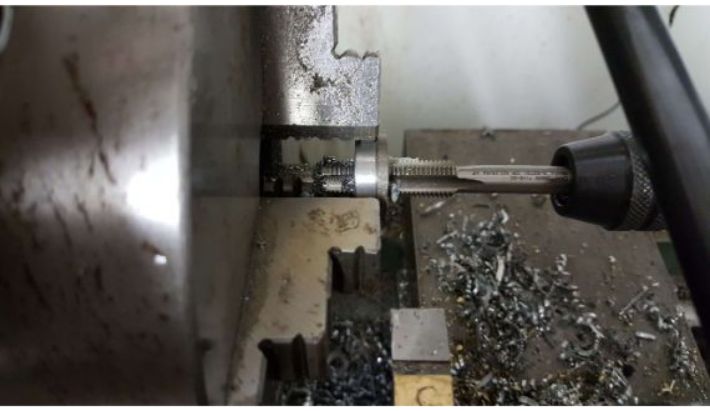
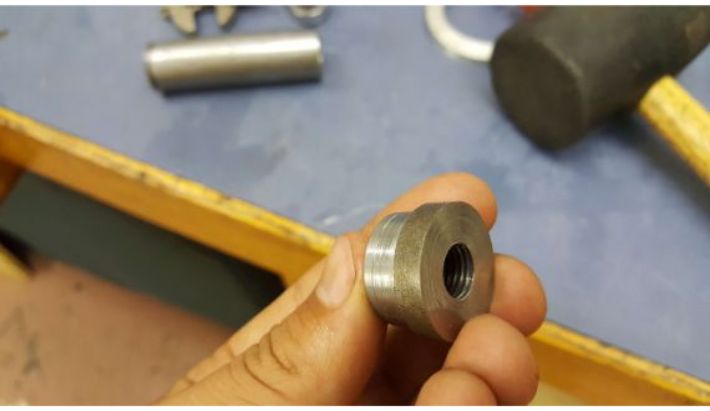
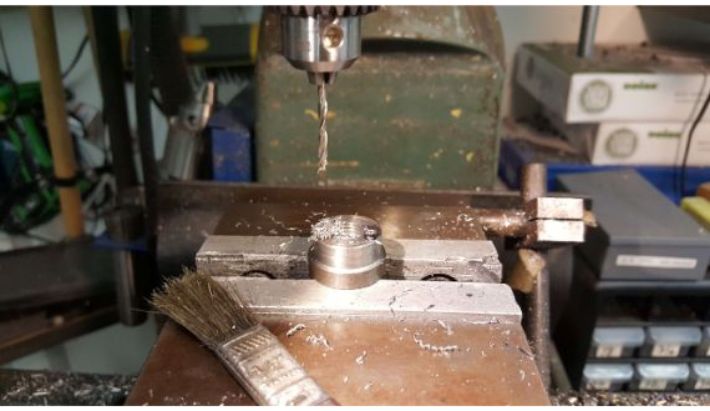
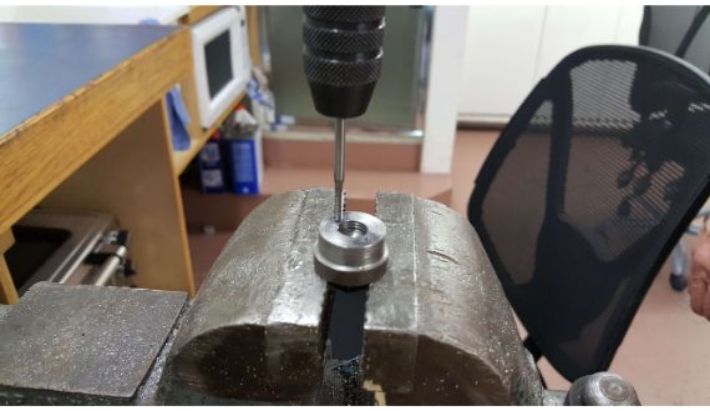
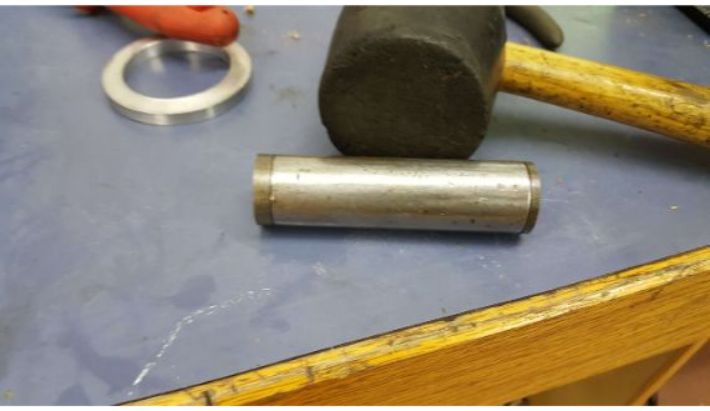
To make the handlebar mounting axle, I turned a shoulder onto a length of 0.5 inch steel hex stock and cut threads around the outside that matched the threads on the endcap. I also drilled a hole through the entire length to fit the throttle cable.
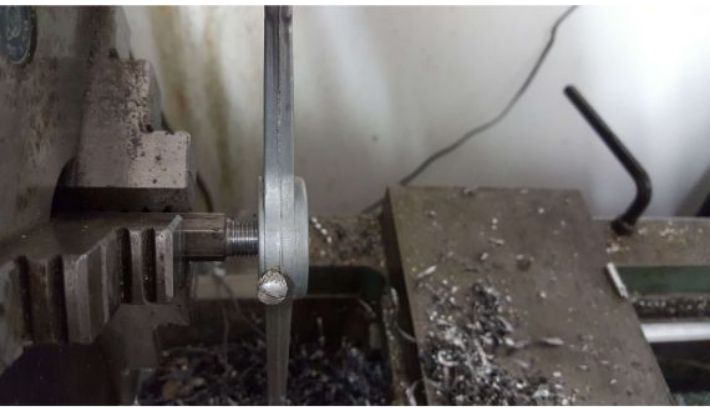
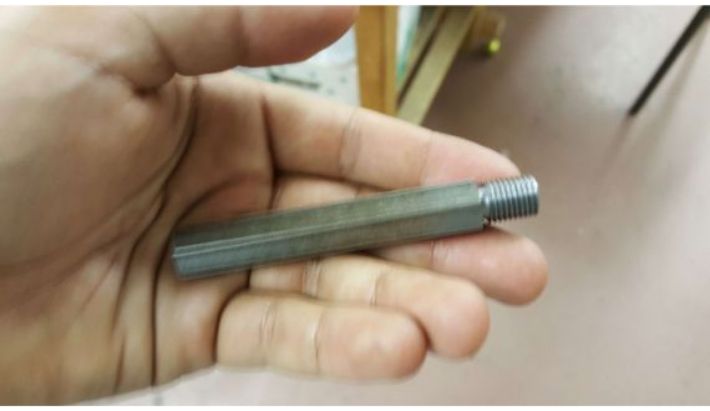
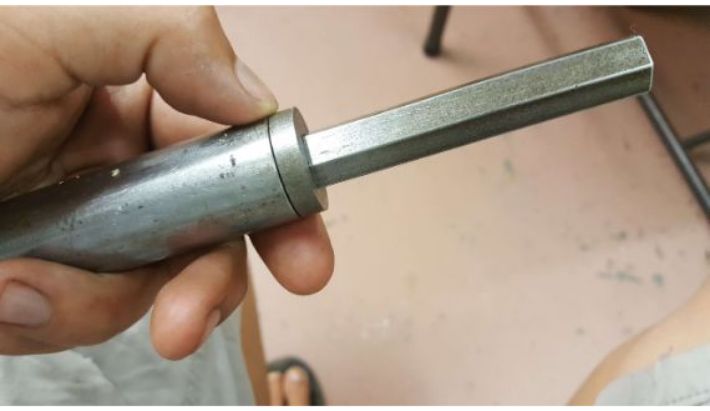
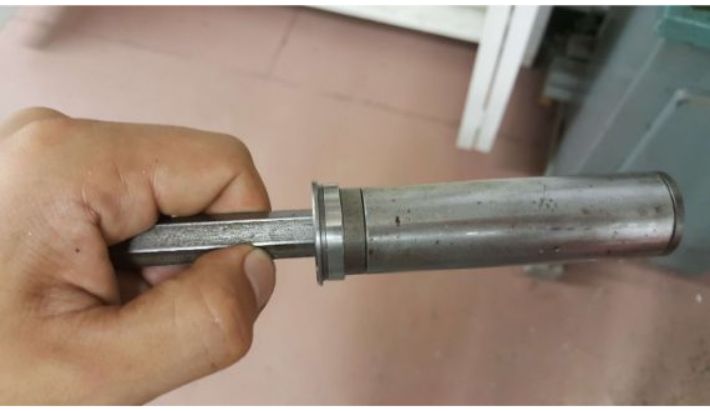
Then, I fabricated the much stubbier bearing mount for the other endcap in the same way as the other, with the slight difference of also internally tapping it 1/4-20 to fit a retaining bolt.
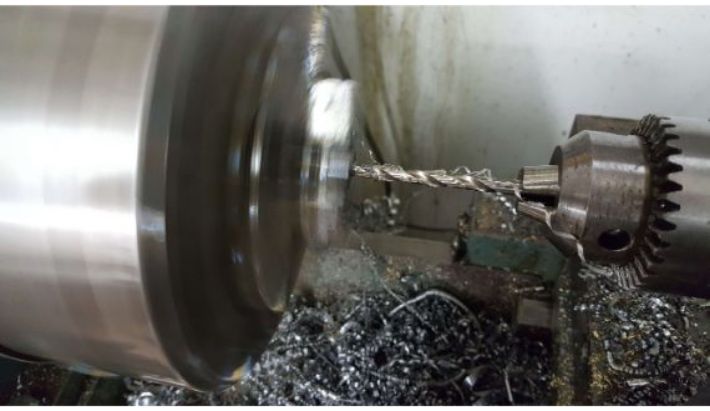
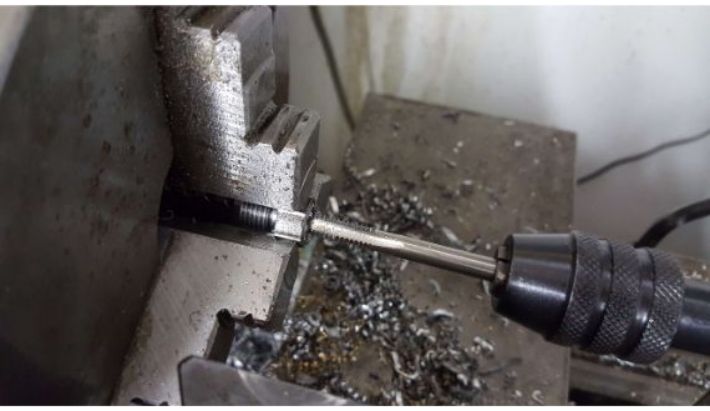
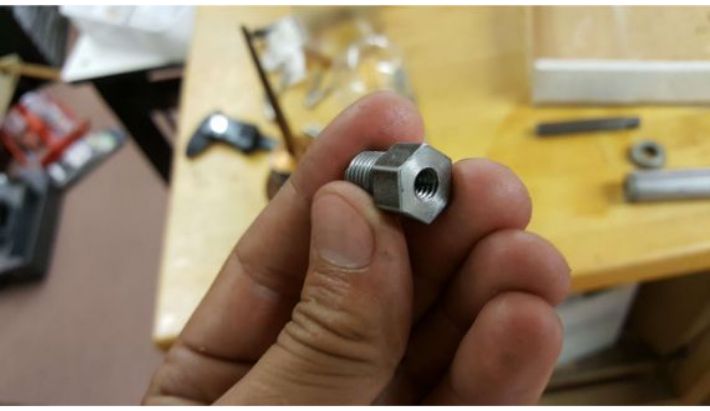
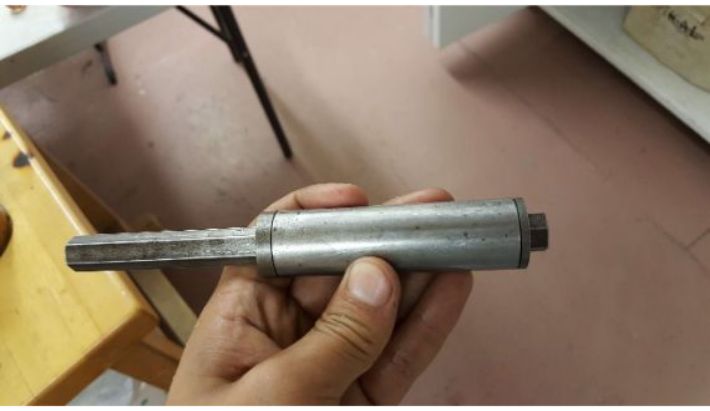
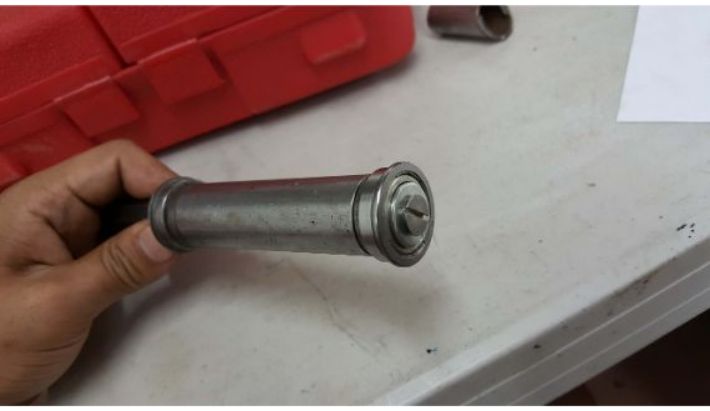
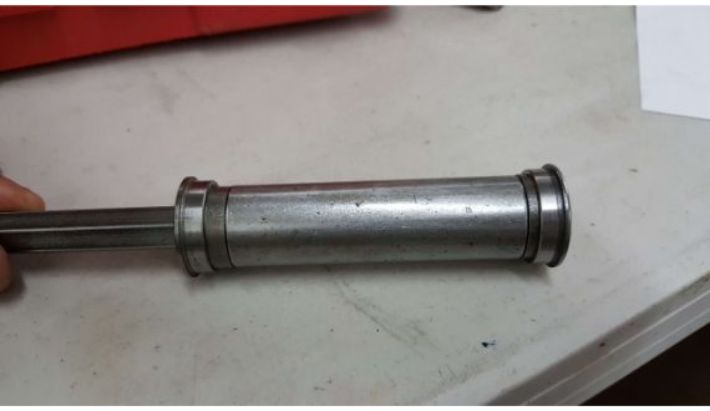
Again, the idea is that the outer slotted shell rides on these bearings. To make the outer shell, I started by turning down some thick wall steel tubing of 1.125 inner diameter. After that, I drilled two offset 0.25 inch holes, and used an angle grinder and a file to cut the slanted slot between them.
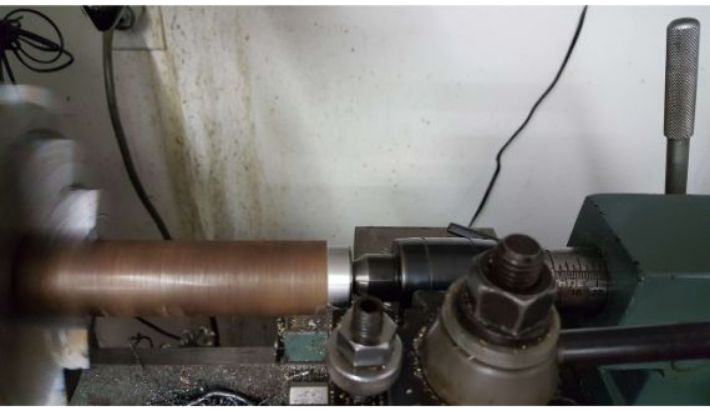
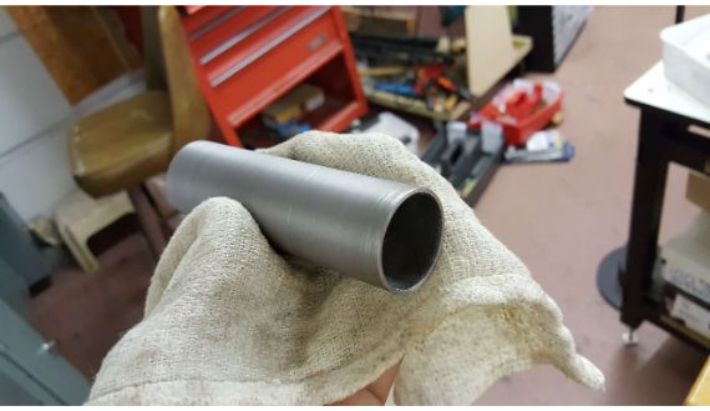
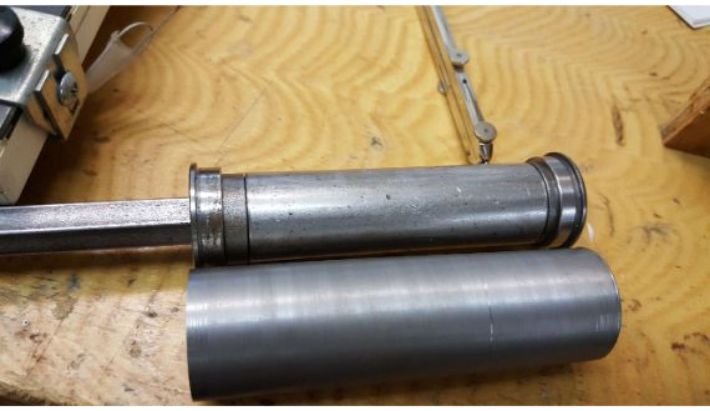
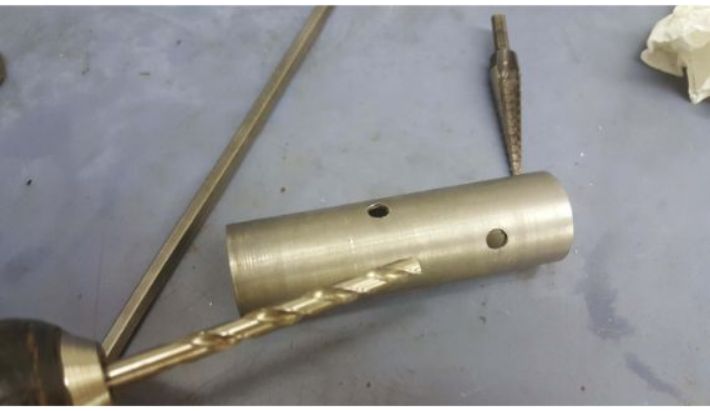
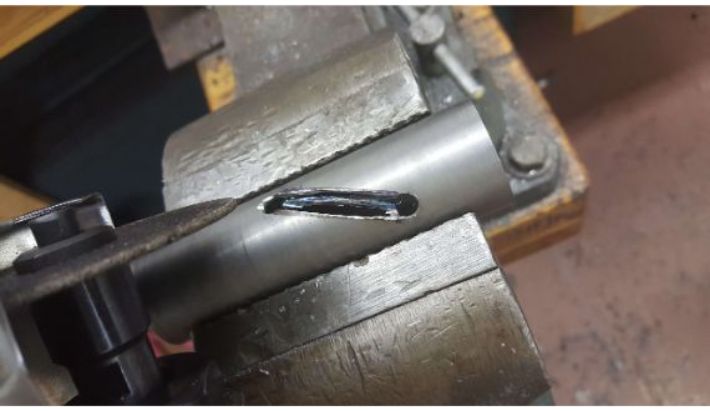
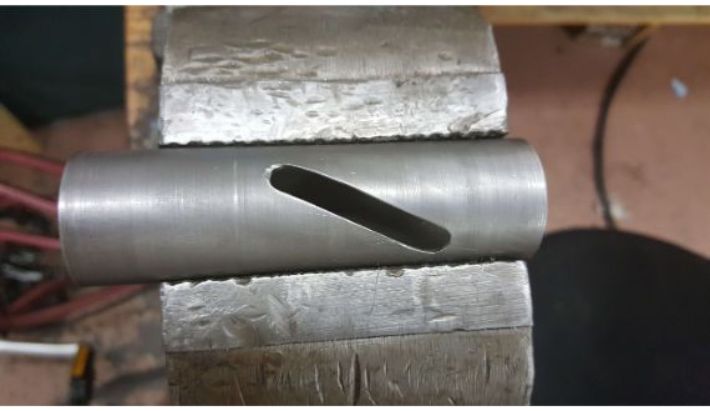
Next, I started fabricating the internal plug. I turned down a slug of steel 0.875 inches in dia. from 1 inch dia. round bar steel stock. I polished it to minimize the friction it would experience on the inside of the internal sleeve. I drilled a hole lengthwise through the center to hold the throttle cable. Then, I drilled and tapped a hole for a 6-32 bolt that would hold down the brass ride peg. Finally, I turned some brass stock down to 0.25 inch dia., and drilled to fit the bolt.
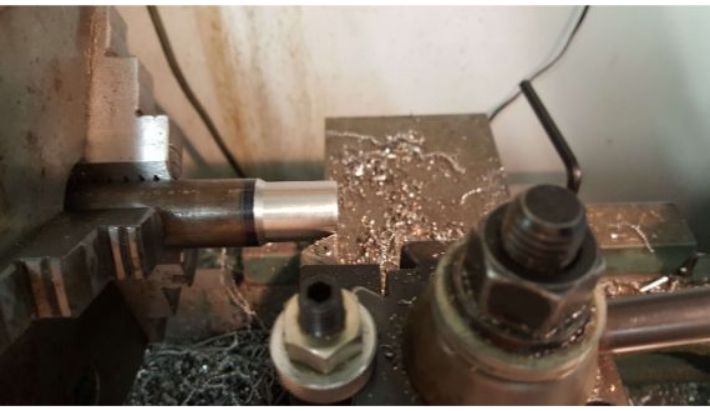
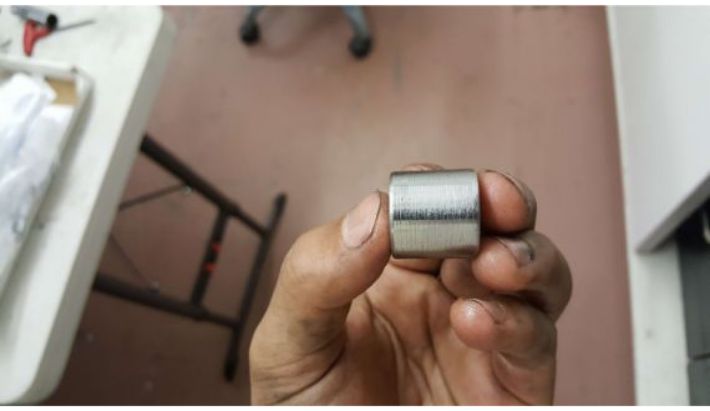
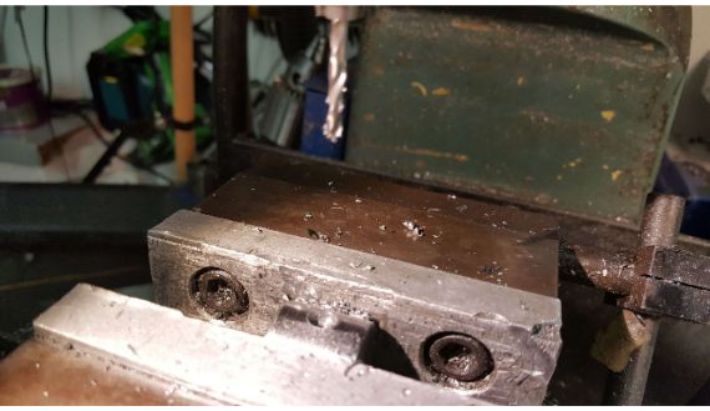
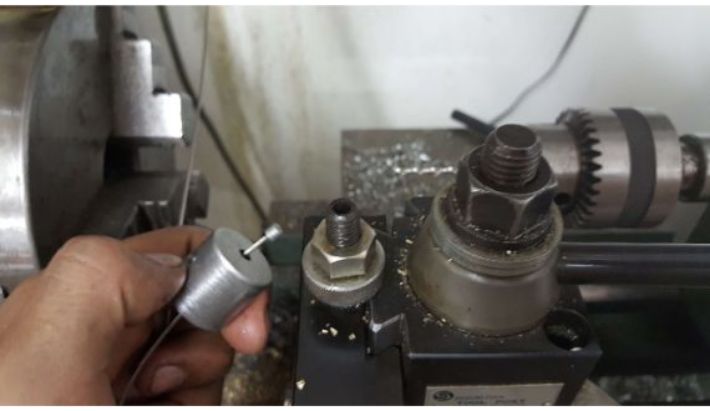
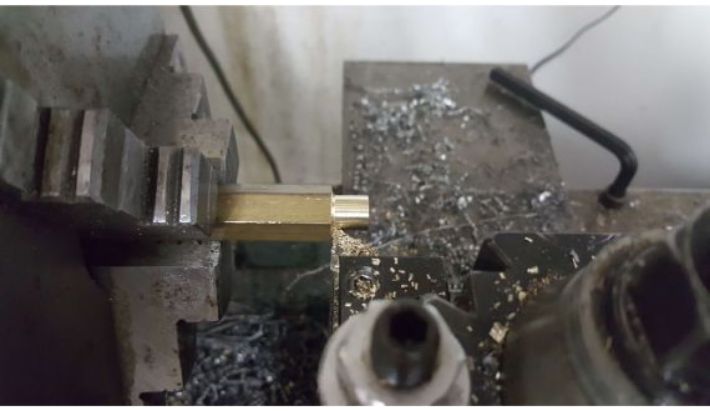
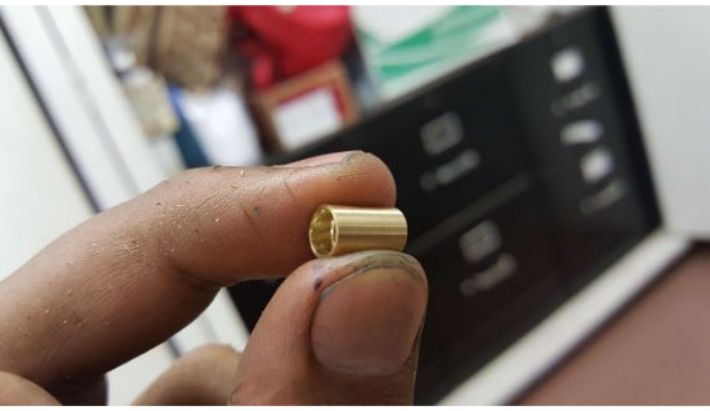
To mount the throttle assembly to the handlebars, I first had to cut a chunk of the right handlebar off to compensate for the extra length of the throttle.
Cutting off a piece of the handle bar.
To actually fit the mounting axle into the handlebar, I had to make a spacer. I just turned down some aluminum stock to fit in the handlebar and drilled a hole in it to fit the mounting axle.
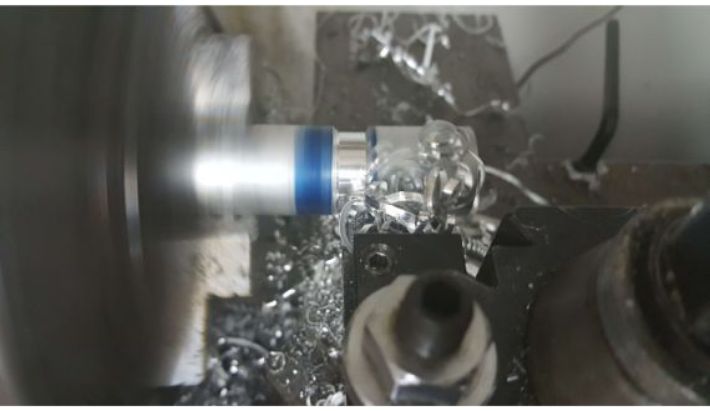
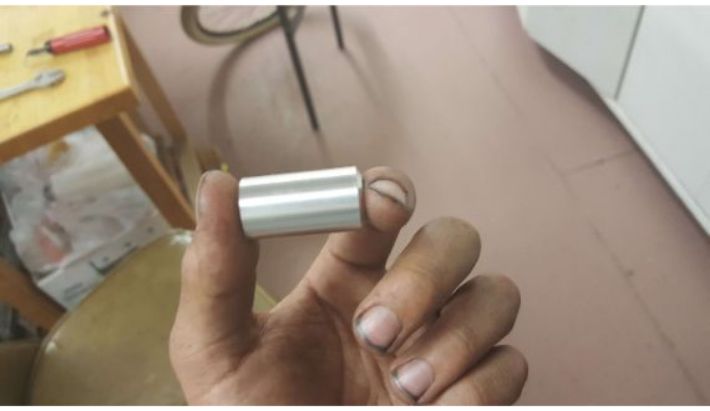
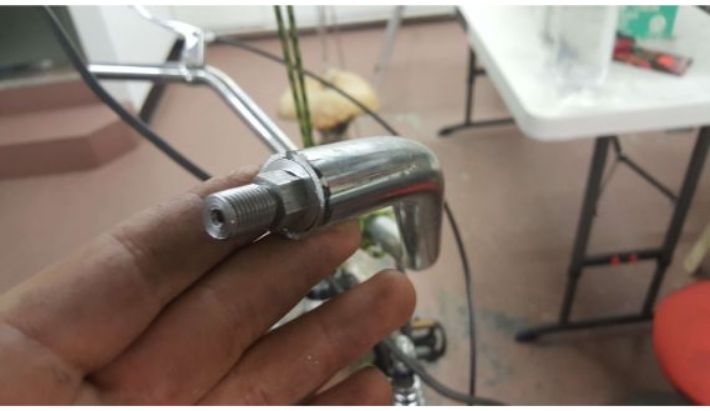
To hold everything in place, I drilled a hole through all of the parts and tapped it to fit a 6-32 set screw.
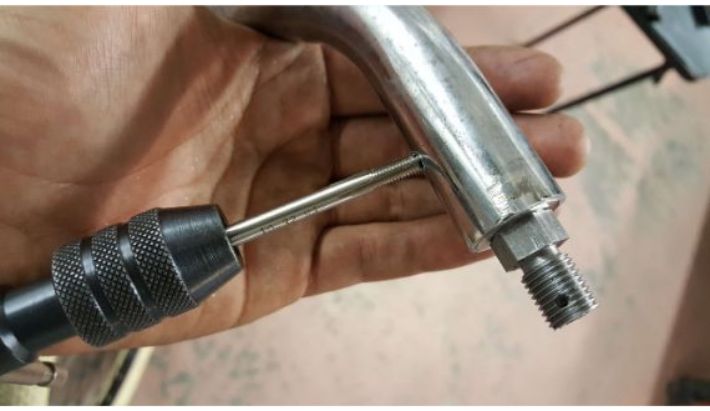
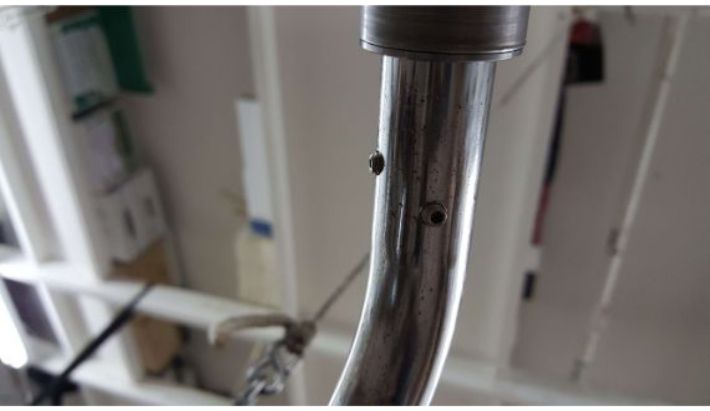
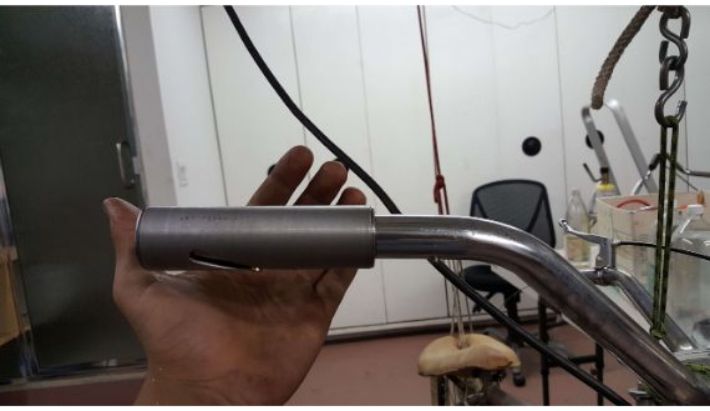
For cable routing, I drilled a hole at the base of the handle bars and inserted a rubber grommet to prevent the cable from fraying on the hole's edges.
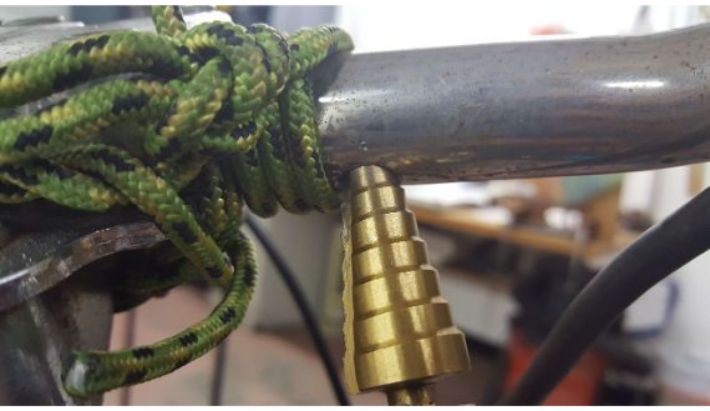
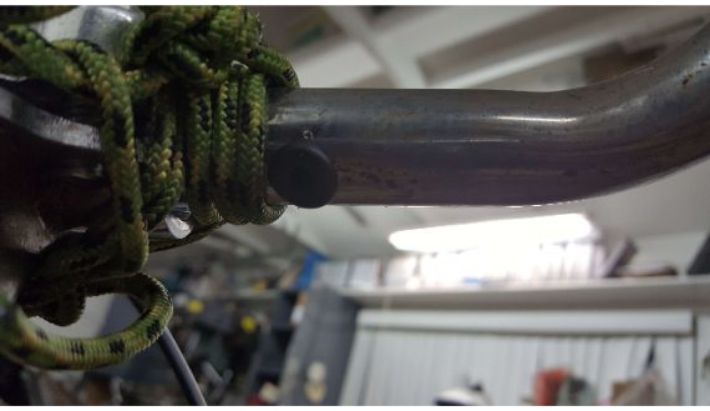
The Engine
I got the engine for this project from an old edge trimmer. Its a Briggs and Stratton 3hp 4 stroke engine. The first thing I did with it was getting rid of shroud so I could install my own pedal start. This left the flywheel exposed, introducing the risk of getting my leg turned into ground meat by the cooling fins. So I chopped those flush with the aluminum magnet holder and then milled them flat. And thats the only big modification I had to make to the engine.
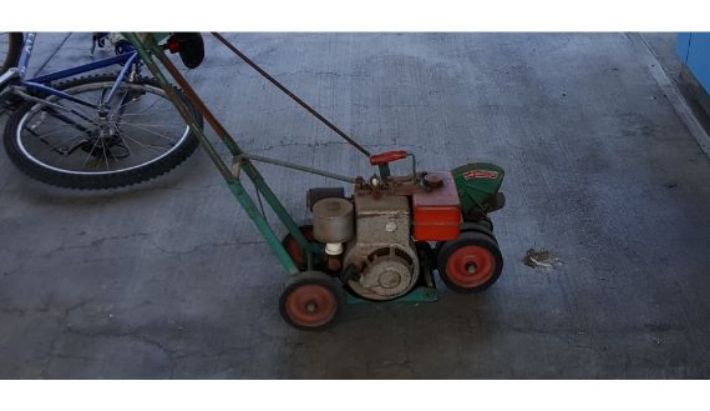
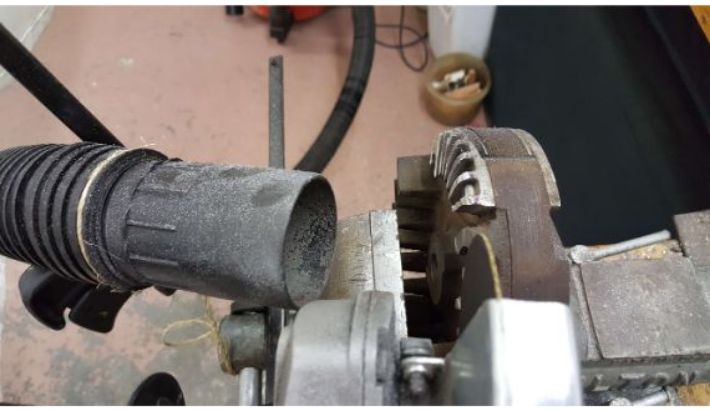
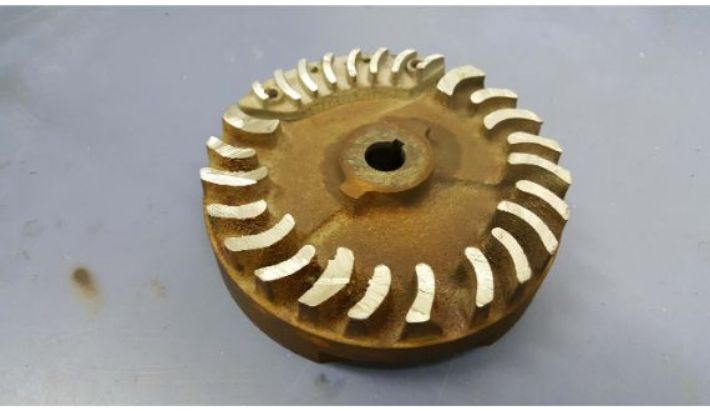
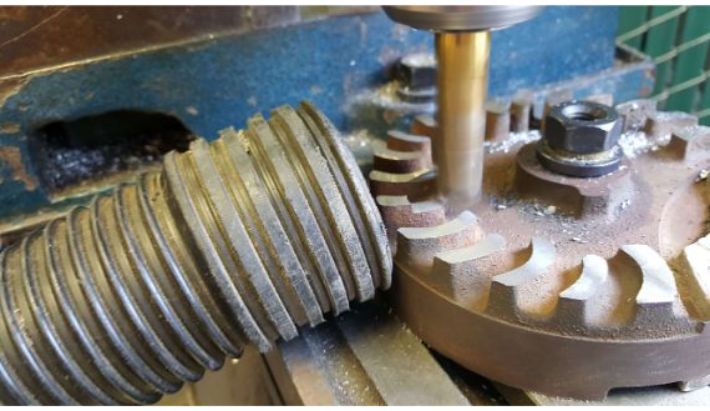
The Exhaust
For the exhaust, I welded an old Briggs muffler to a hotdog style muffler, before welding the body of the system in conduit and elbow bends. Unfortunately, this footage was not captured. I fabricated a pair of matching flanges to act as attachment points for the exhaust setup, and allow me to remove the exhaust if I need to.
I made the flanges out of some scrap 0.125 inch plate, and welded pipe threading to them to match the pipe fittings that come off of the engine's exhaust port. I started by cutting and grinding them to shape, and then drilled matching holes in them. Unfortunately that footage was lost as well. I then tapped the outer holes to accept the 6-32 bolts that keep the flanges pressed together.
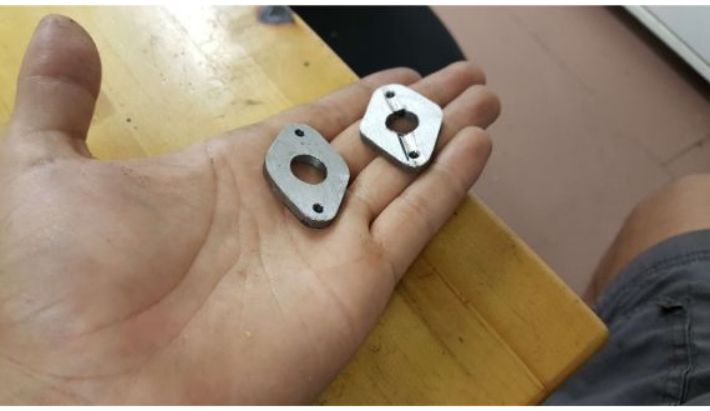
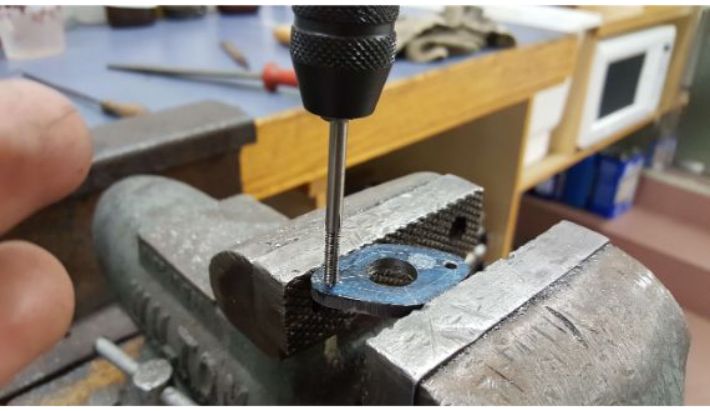
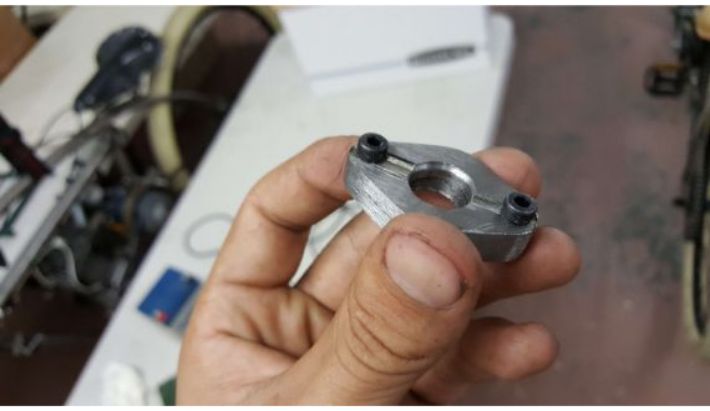
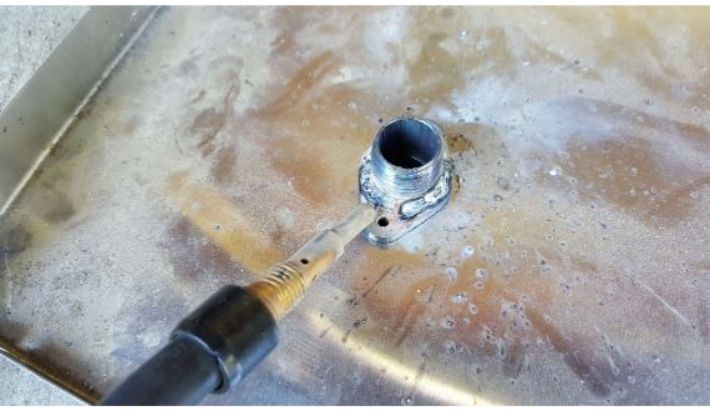
One flange was welded to pipe thread to screw into the elbows coming off of the engine, and the other flange was welded direct to the exhaust line.
To mount the exhaust to the frame of the tracker, I fabricated a threaded insert to be welded to the down tube out of some 0.375 inch dia. steel round bar.
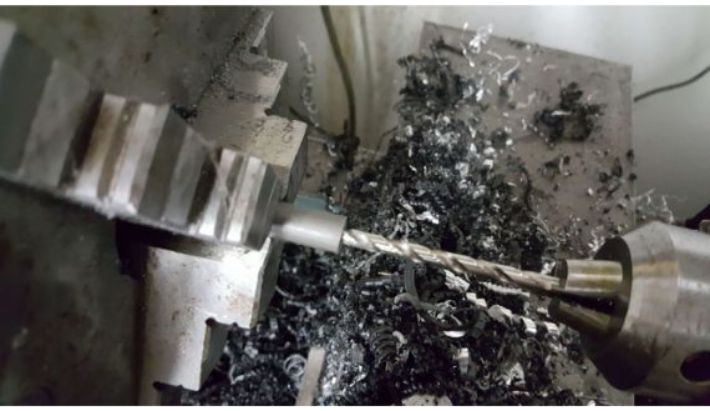
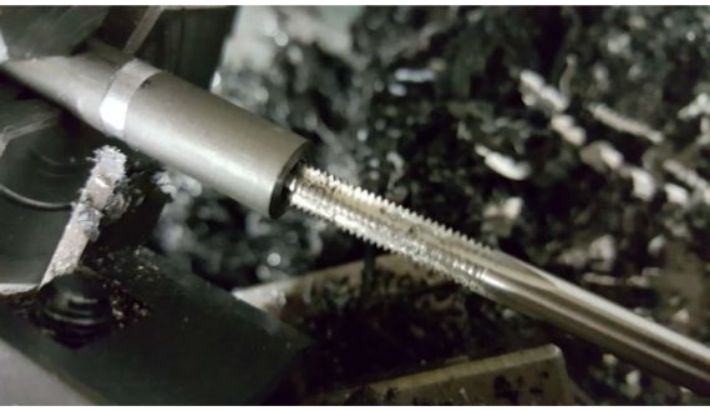
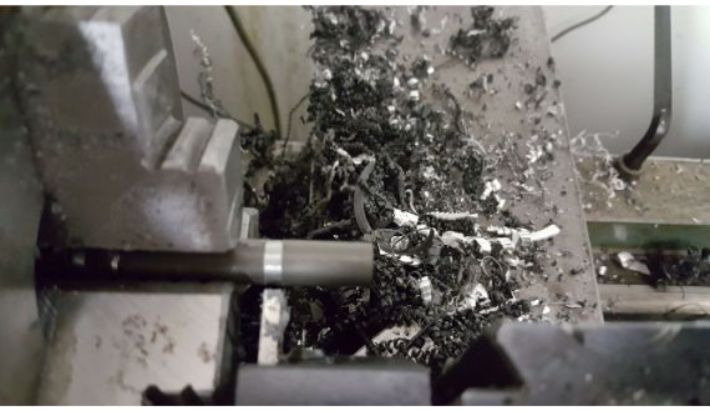
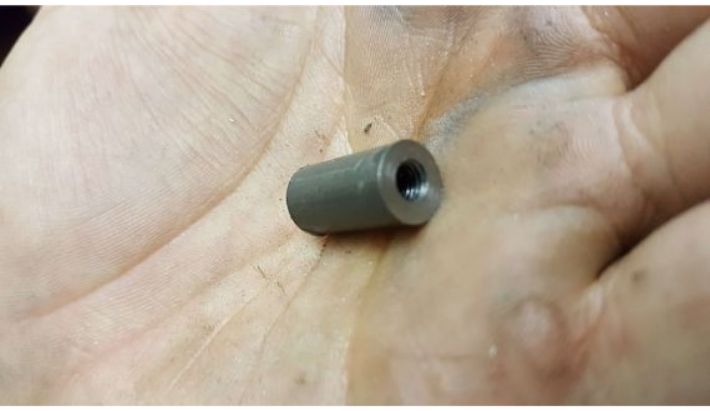
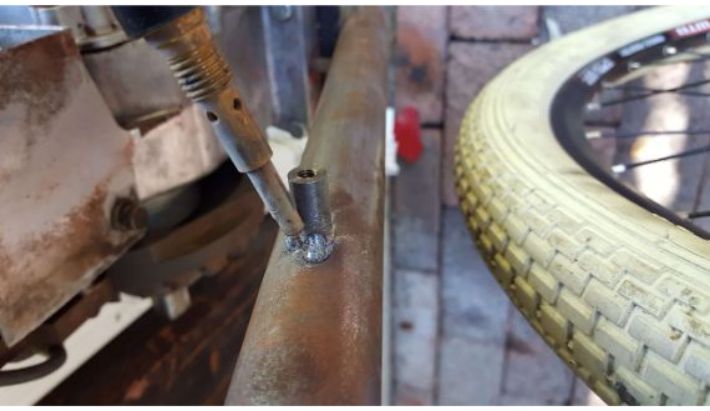
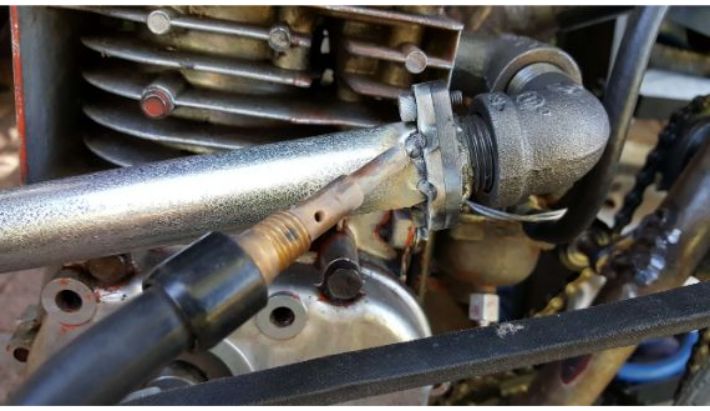
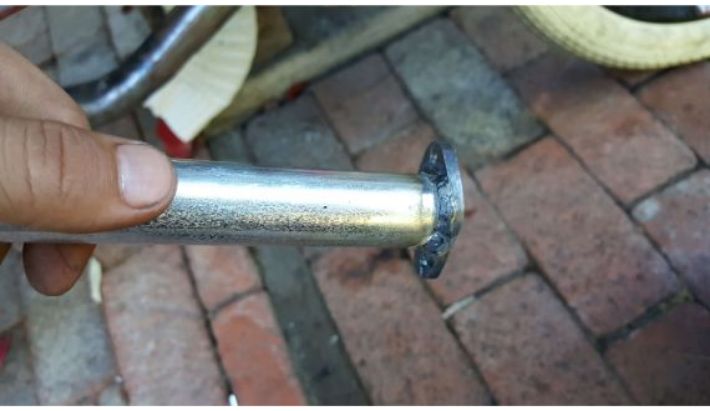
I then welded a tab with a hole drilled into it to the exhaust, so it could be bolted to the insert.
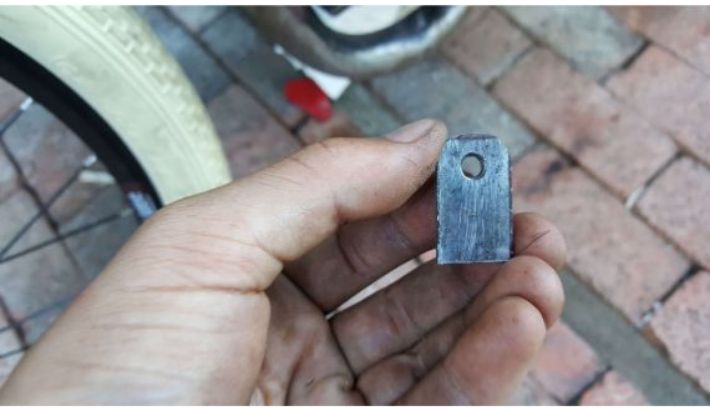
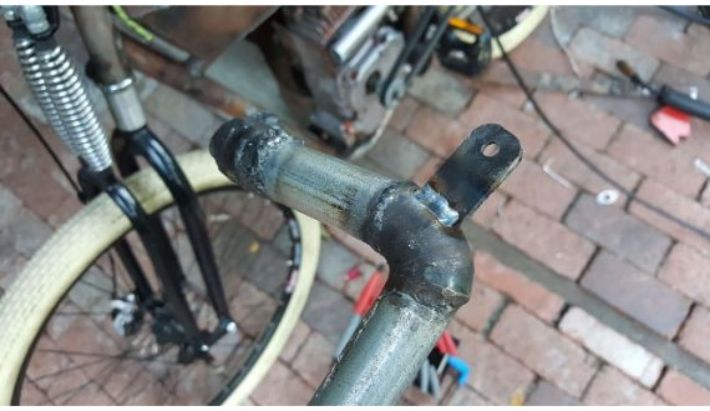
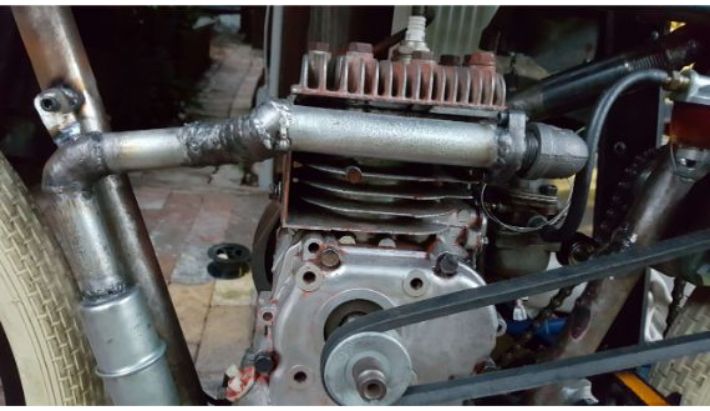
The Bottom Bracket
To fit the pedal start system that I wanted, I had to lower the position of the bottom bracket so that the chainring could clear. To do this, I hacked a bottom bracket off of a kids bike and welded it in the position I wanted. There was a flat plate right beneath the chain stays that I welded standoffs to in order to hold the bottom bracket shell at the proper position.
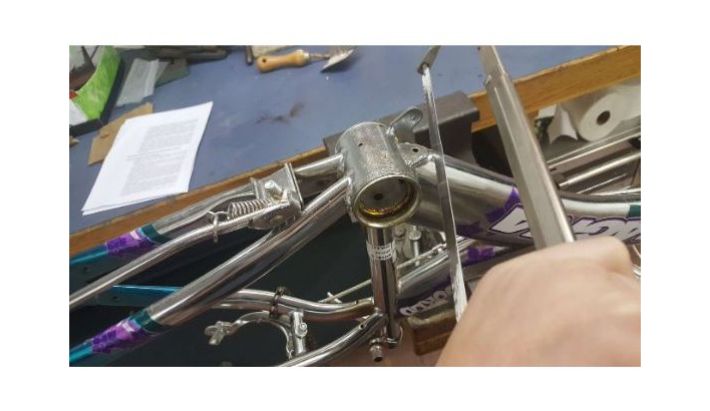
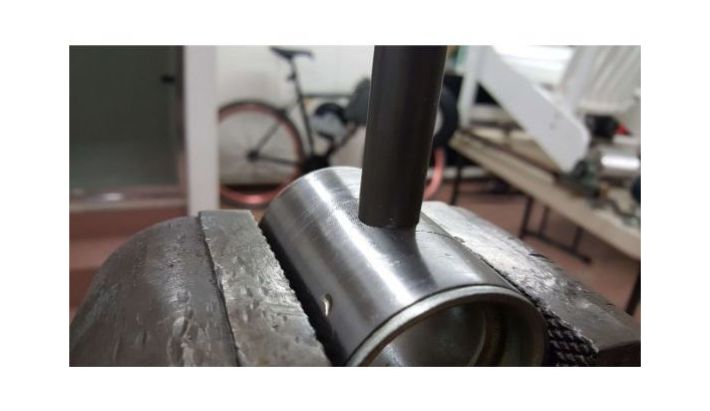
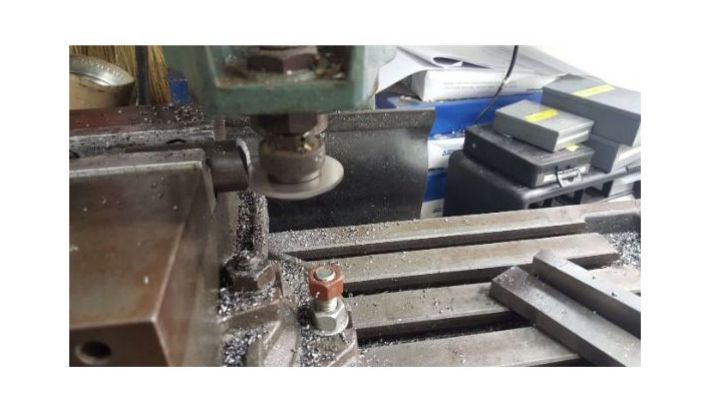
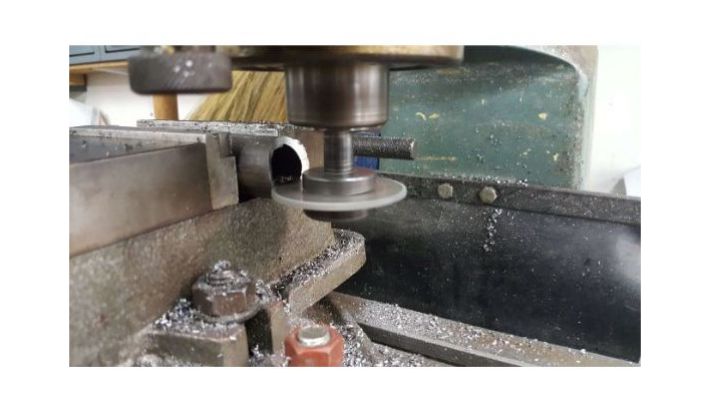
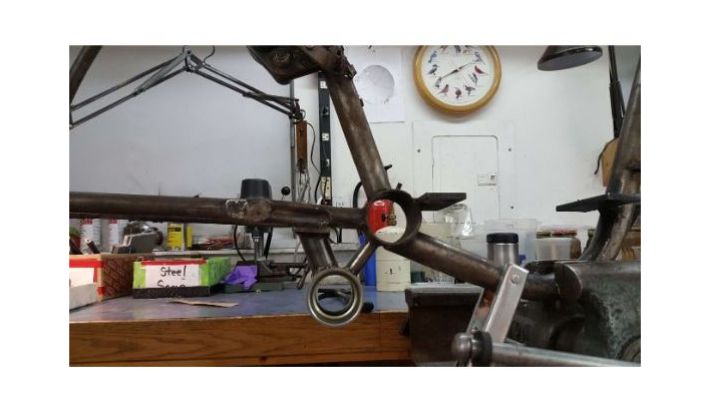
The Pedal Start
With the bottom bracket shell installed, I could proceed with the pedal start system. This was another tricky mechanism to figure out. I wanted to be able to pedal the bike like a normal bicycle, as well as be able to start the engine with the pedals. How was I going to be able to pedal the tracker like a normal bike without kicking the engine over? A freewheel and some pins, basically.
I fabricated an intermediate shaft to be placed between the pedals and the flywheel of the engine, held down just under the engine mounts. The idea was that he pedals would be connected to a freewheel on this shaft that engaged when the pedals are pedaled forwards. This freewheel would be mounted to a free spinning roller hub on the shaft. Just adjacent to this roller hub would be an identical, independent free rolling hub that had a sprocket mounted to it. This sprocket would be linked by chain to another sprocket on the flywheel of the engine. There would be holes drilled in this sprocket to fit steel pins, and matching sleeves would be welded to the other roller with the freewheel attached. These pins would be inserted when I wanted to start the engine, mechanically connecting the freewheel roller to the sprocket roller, allowing the pedals to transmit force to rotate the flywheel.
When I wanted to manually pedal the bike, I could then simply remove the pins, and with the rollers no longer mechanically connected, I could pedal without transmitting any force to the flywheel.
I began the fabrication by making a freewheel hub out of some aluminum. I cut threads in the stock to allow the freewheel to thread right on. I then drilled a hole in the aluminum so it could fit over the 1 inch dia. steel tube I was using for the roller stock. I put two set screws in the aluminum hub to fasten it to the roller.
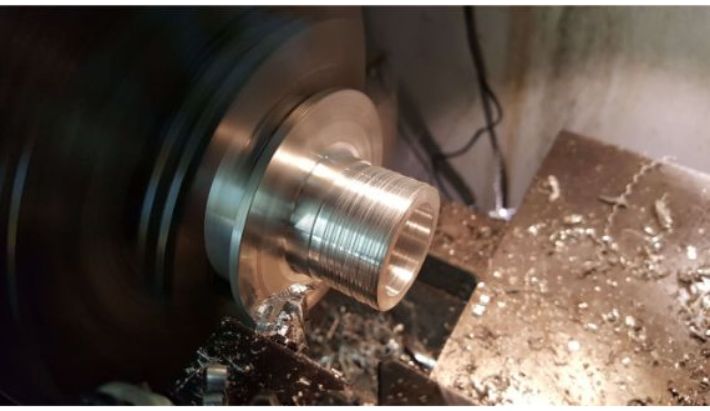
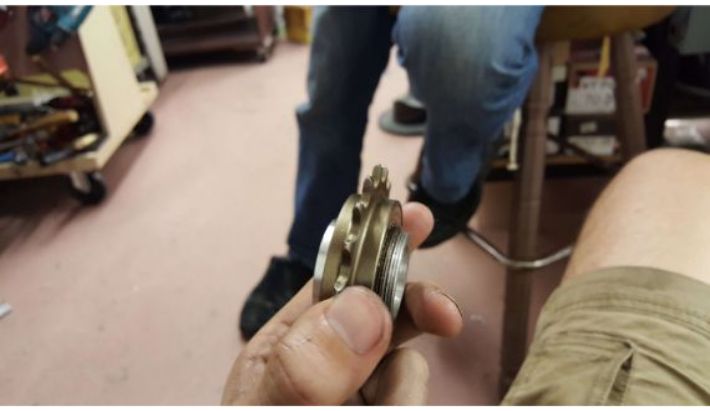
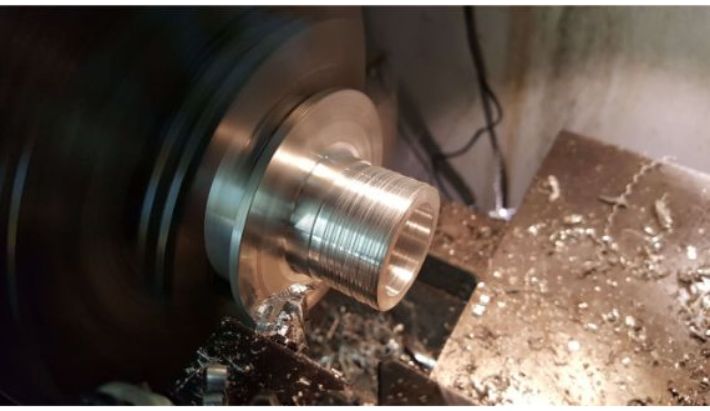
Then, I fabricated the intermediate shaft. I started by cutting a length of 2 inch wide by 0.25 inch thick steel bar the same width as the engine mounts. Then, I drilled matching bolt holes in the bar. I then cut three lengths of 0.5 inch dia. steel round bar, two short peices the same size to act as standoffs, and one long piece that I tapped 1/4-20 on one end for the shaft itself. I welded the standoffs to the steel bar, then the shaft to the standoffs before bolting it into under the front engine mount.
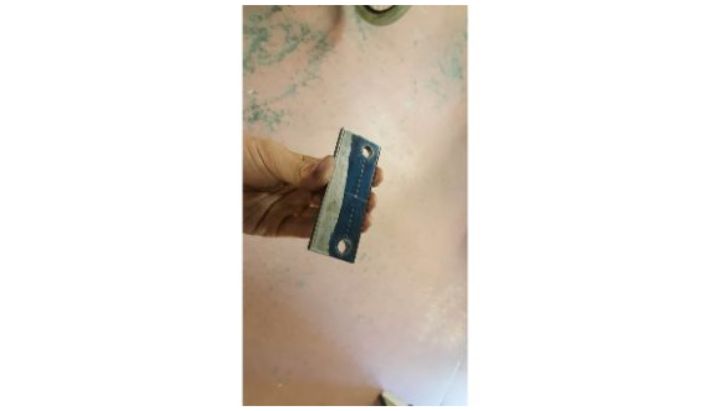
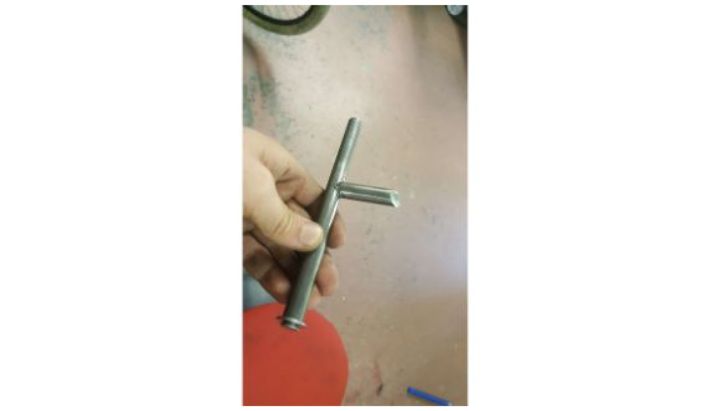
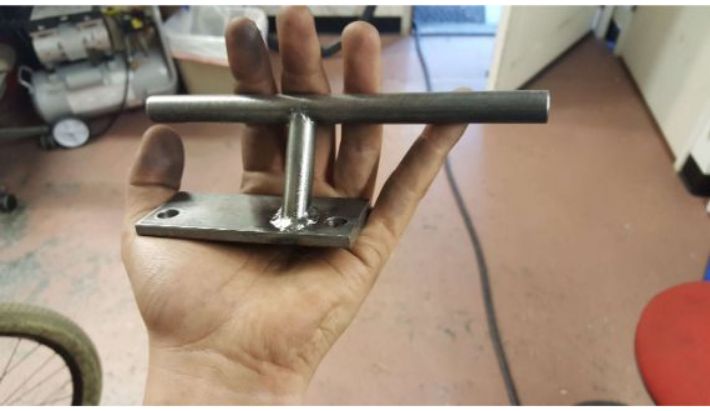
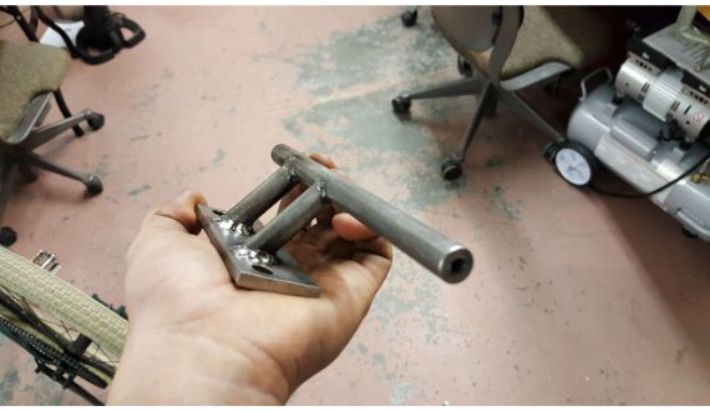
I then bored a #25 chain sprocket to fit the same diameter roller as before, and attached it with set screws to a roller similar to the one holding the freewheel. The rollers were pretty simple, just the 1 inch tube with 0.5 inch ID bearings inside them to fit the shaft.
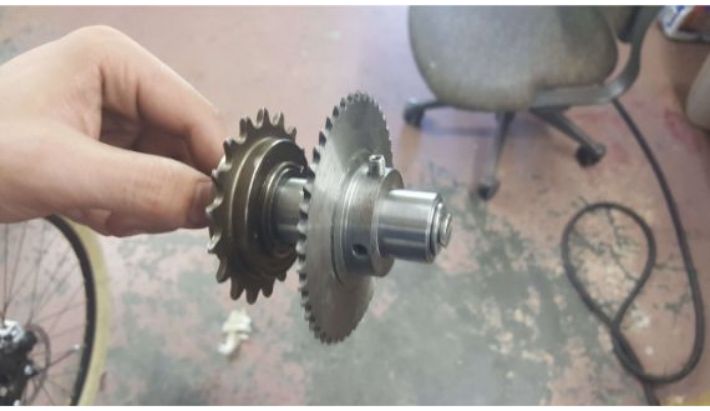
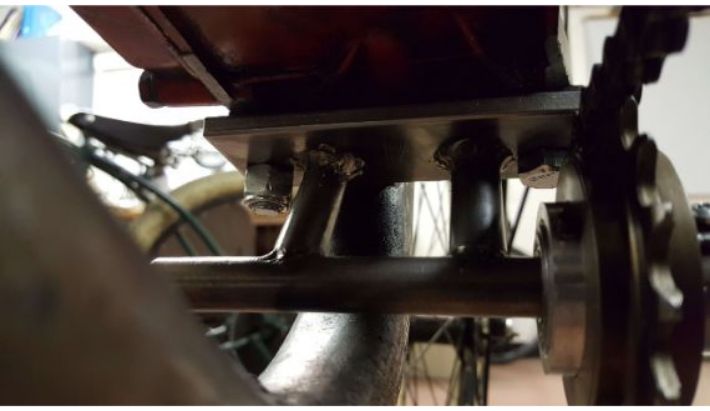
Next, I had to mount a bike sprocket to the chainring and crank set that I was using for the pedals. This sprocket would be the one connecting the pedals to the freewheel. To mount the sprocket, I turned a hub on the lathe out of aluminum and bolted the sprocket right to it. Then I bolted the hub to the chainring/ crank assembly. The chainring/crank assembly was pulled from the same kids bike that I took the bottom bracket from (I needed short kids cranks to clear the flywheel)
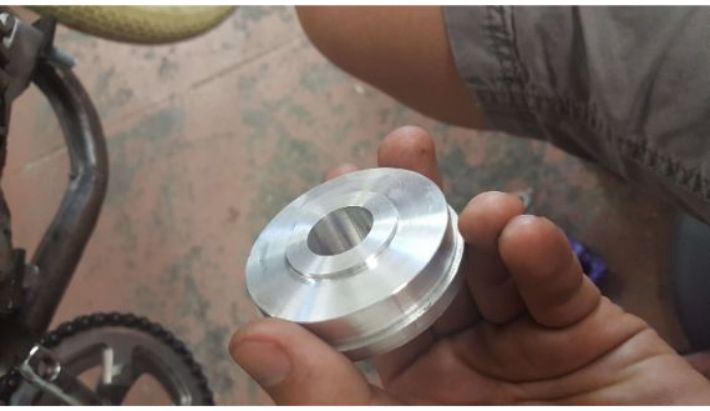
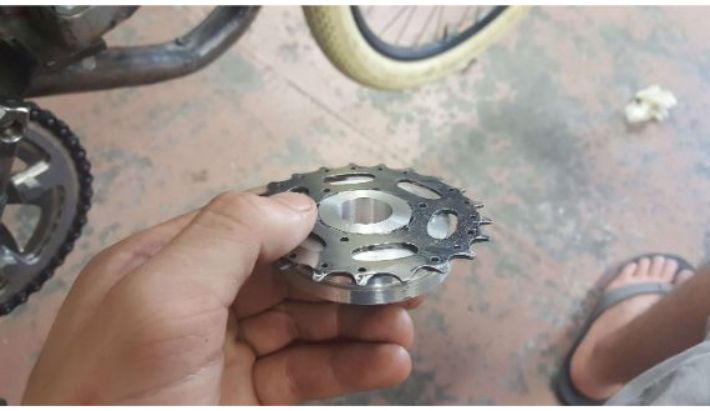
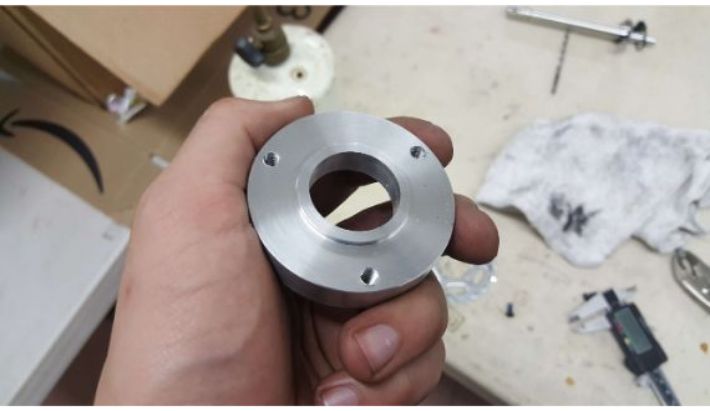
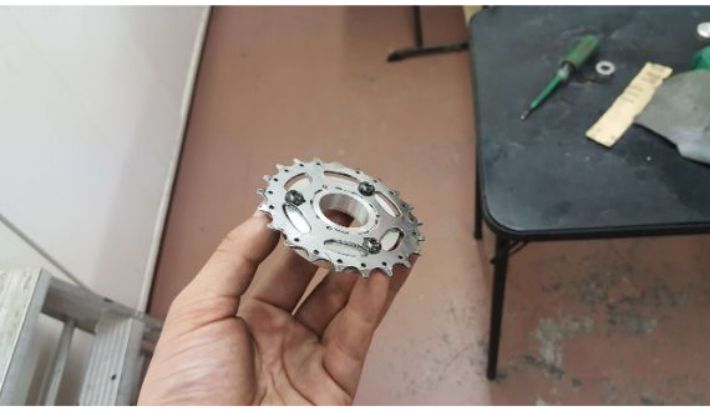
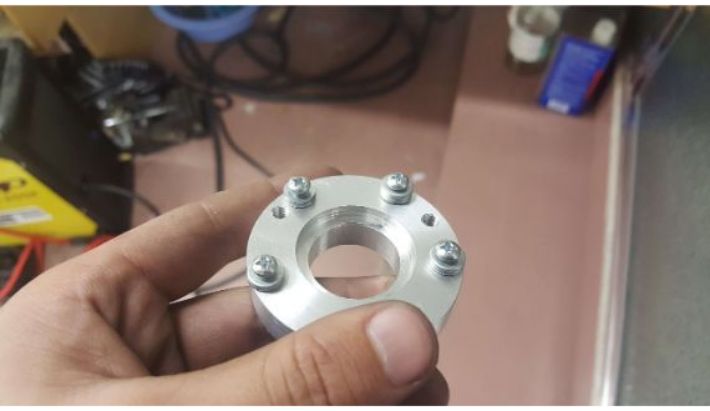
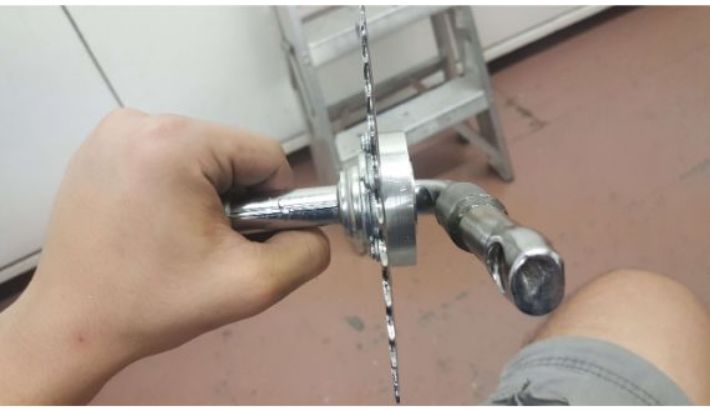
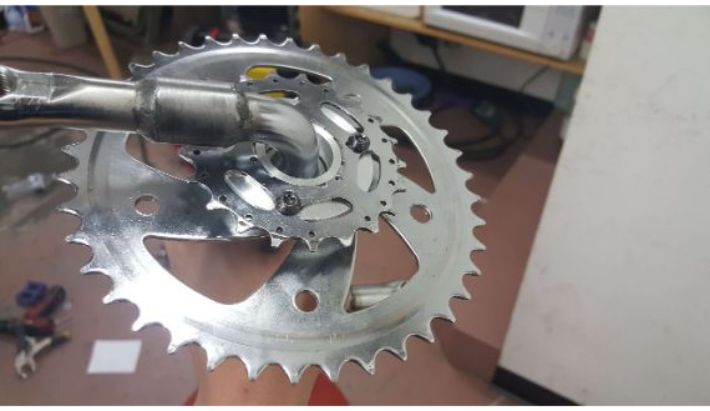
To replace the original pull start, which also acted as a nut holding on the flywheel, I tapped a small #25 sprocket to serve the same purpose. This sprocket connected to the sprocket on the pedal start shaft via chain. To prevent this sprocket from coming unthreaded, I turned an aluminum sleeve to go over the crankshaft. I tapped the crankshaft, and then bolted the spacer on.
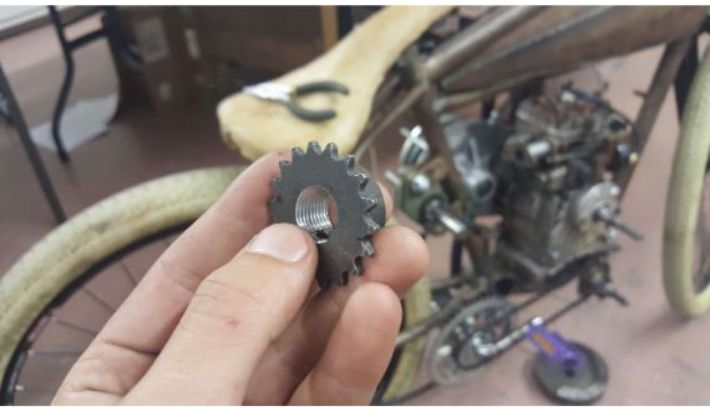
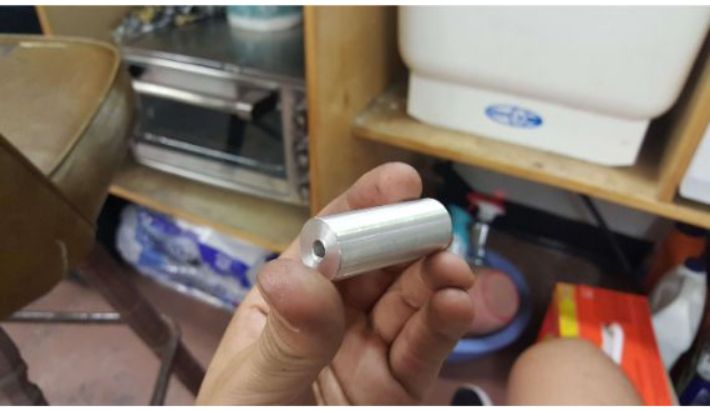
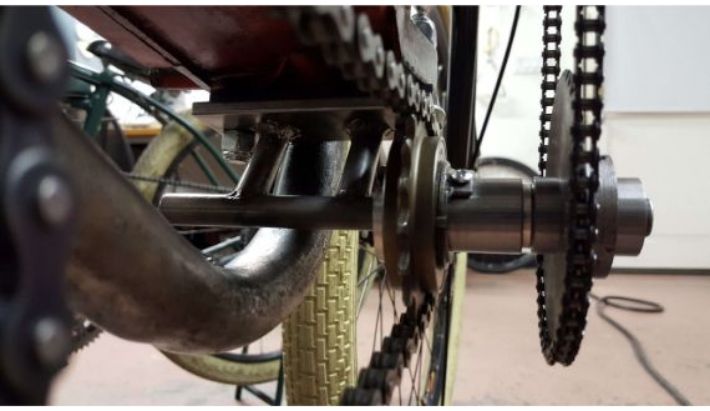
The Track Stand
Another classic part of the board tracker aesthetic is the trackstand. The trackstand not only supports the bike when it is not in motion, it also suspends the rear wheel and so allows the rider to start the engine more easily. I fabricated it completely out of 0.625 inch dia. steel round tube. I cut a bunch of lengths and welded them together for the basic frame, and then turned some brass bushings for the stand to pivot on. The pivots allow the stand to swing up around the wheel to rest behind the seat when not in use. To mount the stand to the bike I had to weld extensions to the dropouts. These extensions were then drilled and tapped 1/4-20, and the stand could then be bolted on. Finally, "Y" arm supports were welded to the track stand, and hard stop pegs were added to the chain stays.
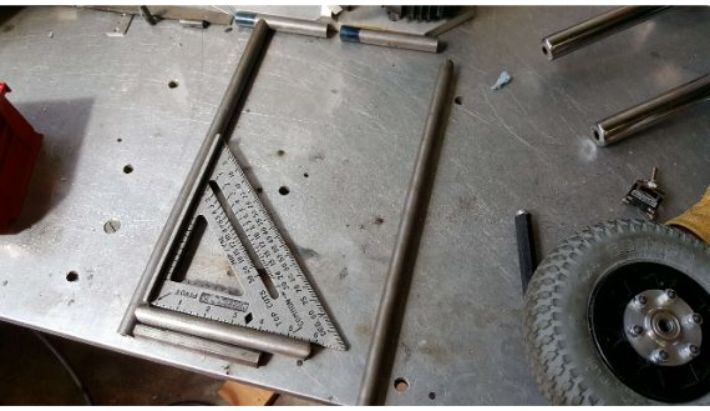
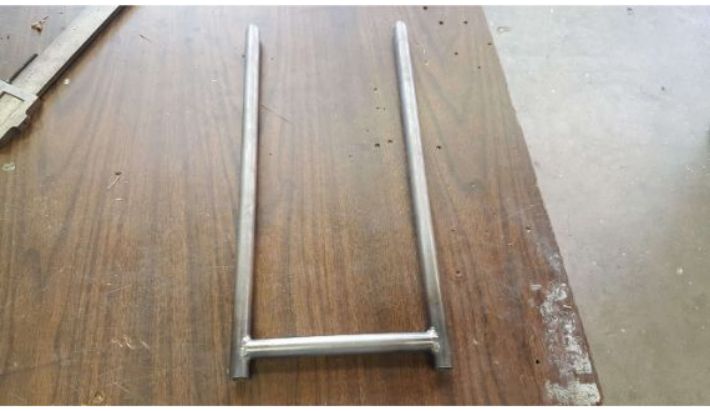
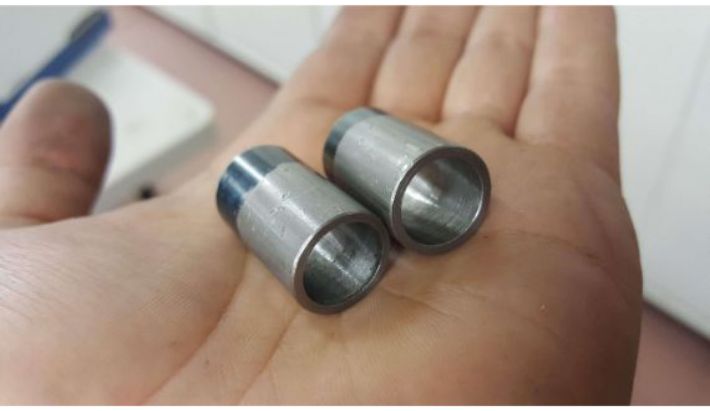
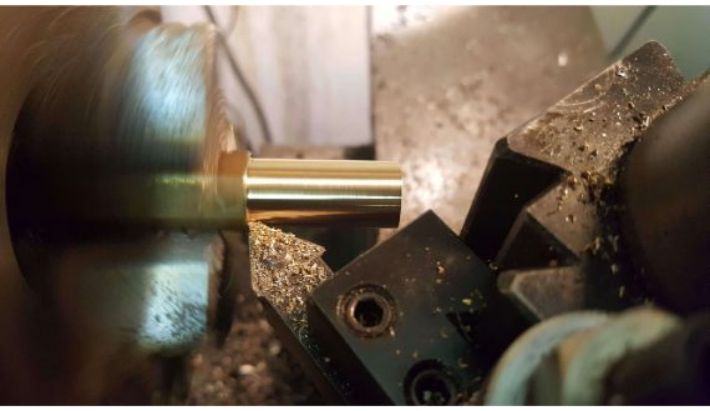
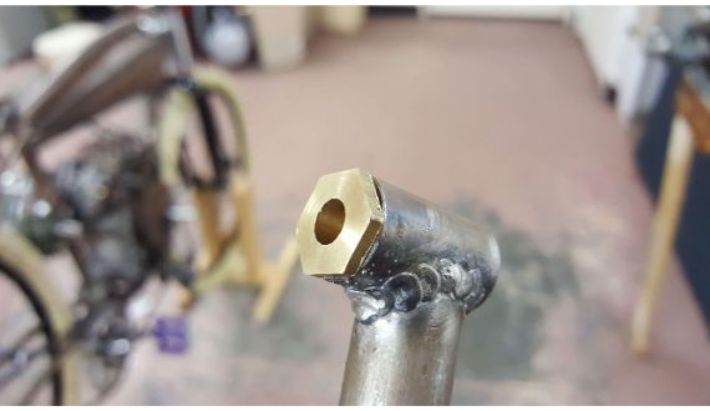
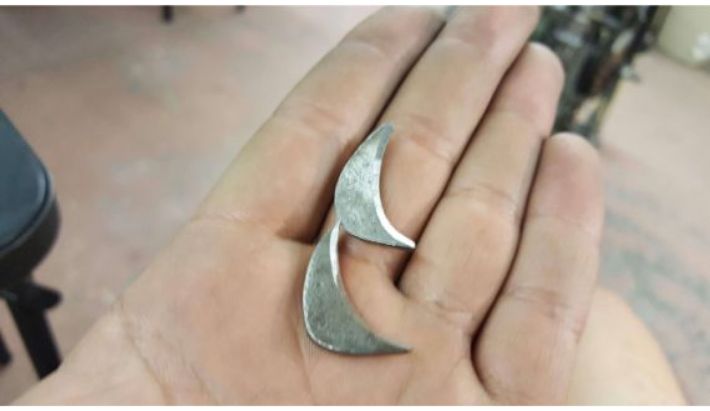
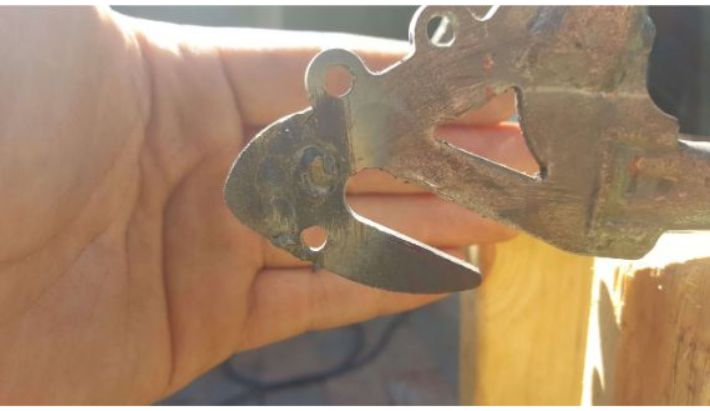
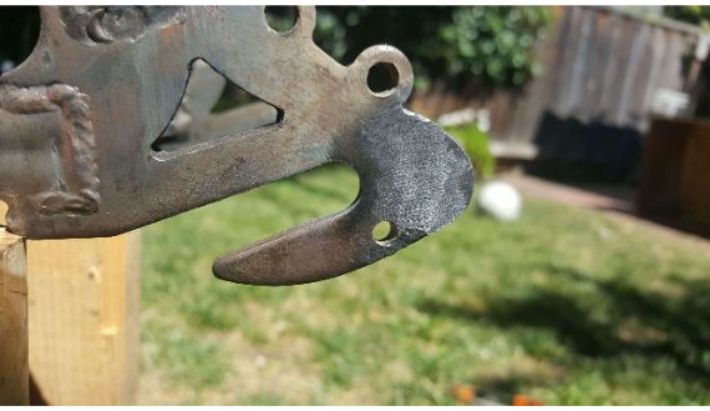
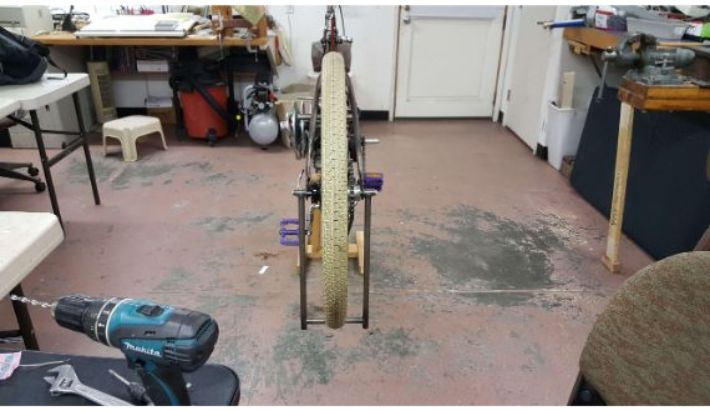
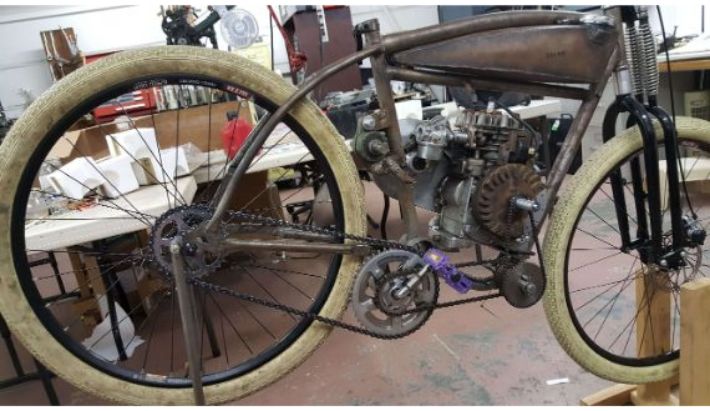
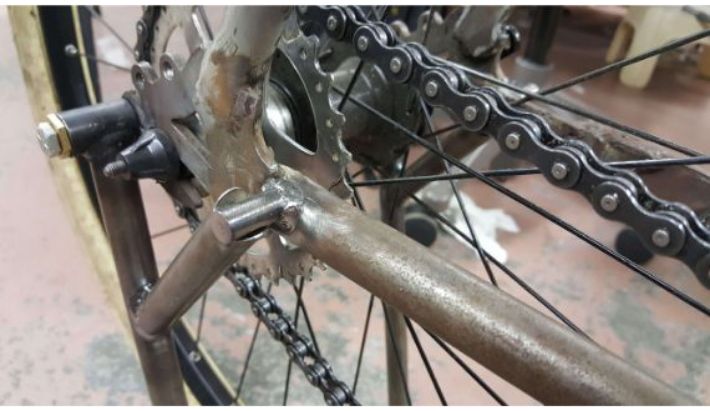
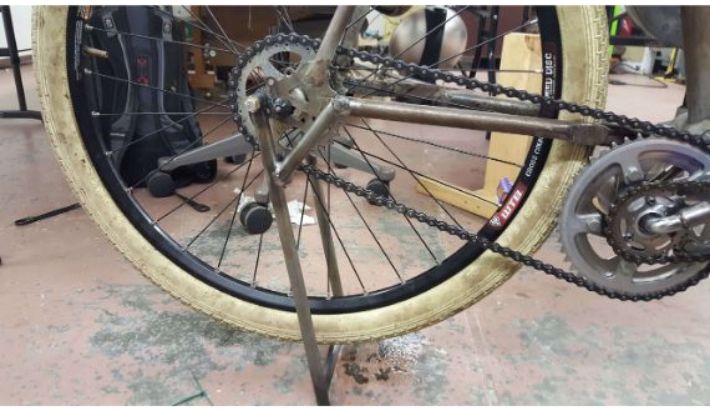
The Jackshaft
Finally, we revisit the jackshaft, which has since been cut to length and keyed. The main purpose of the jackshaft is to provide an additional gear reduction between the torque converter and the wheel. However, since the drive chain is connected to the wheel via sprocket, force is applied through it to the torque converter to the crankshaft, essentially nullifying all the freewheel work in the pedal start that was supposed to fix the problem of accidentally starting the engine when trying to pedal normally. So, not only did I have to make a hub for the sprocket for the reduction, I had to make it a freewheel hub to prevent force from being transferred from wheel to crankshaft.
To make the freewheel hub, I turned two discs of aluminum that could sandwich a bicycle frewwheel. I then drilled holes in these rings between the teeth of the freewheel so I could run bolts through the discs and prevent the freewheel from rotating. I filled the gaps between the bolts and the teeth with aluminum spacers. Then, I centered this hub on the reduction sprocket, and drilled and tapped matching holes to mount the hub. Finally, I took the jackshaft drive sprocket and thread cut the outside of it to thread into the inside of the freewheel.
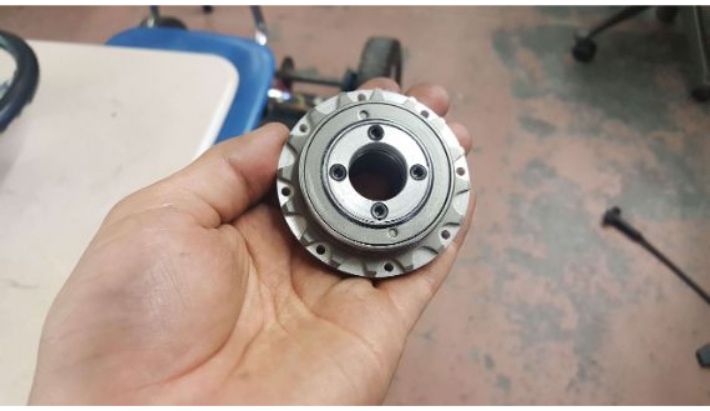
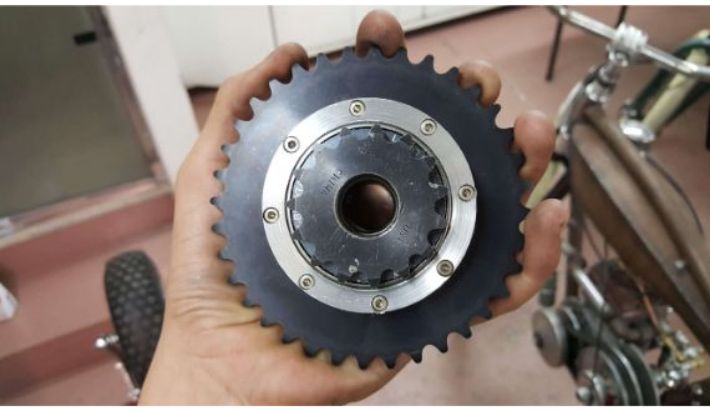
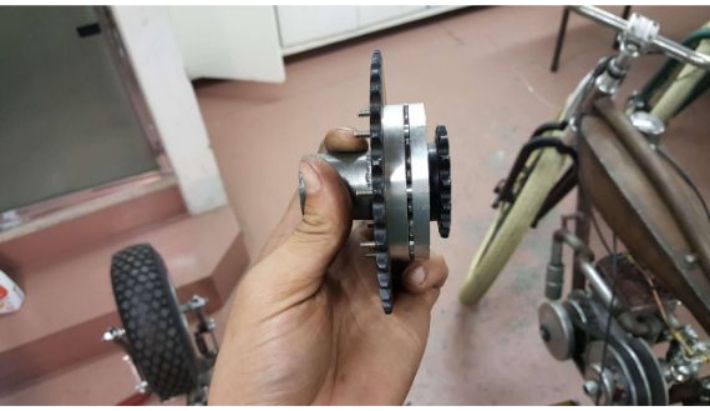
To keep the jackshaft drive sprocket from unthreading, I made a steel bearing support that presses between the sprocket and the flange bearing supporting the jackshaft, blocking it from coming out.
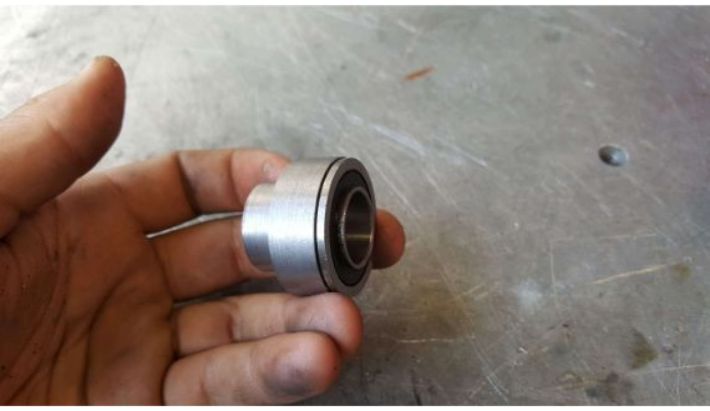
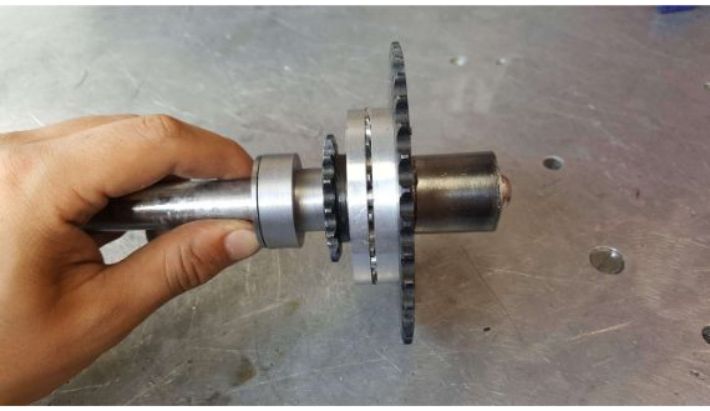
And that concludes the build! This thing took two years to complete, what is uploaded here is the footage of the successful iterations. There were two full other iterations that failed before this successful one. The reason why some footage is missing is that towards the end, I had less confidence that what I was working on would work, and so I took less pictures anticipating failure. My perseverance payed off! The tracker is a blast to ride, and it goes about 30-35mph. It also looks and sounds super cool. Thanks for sticking with the build!
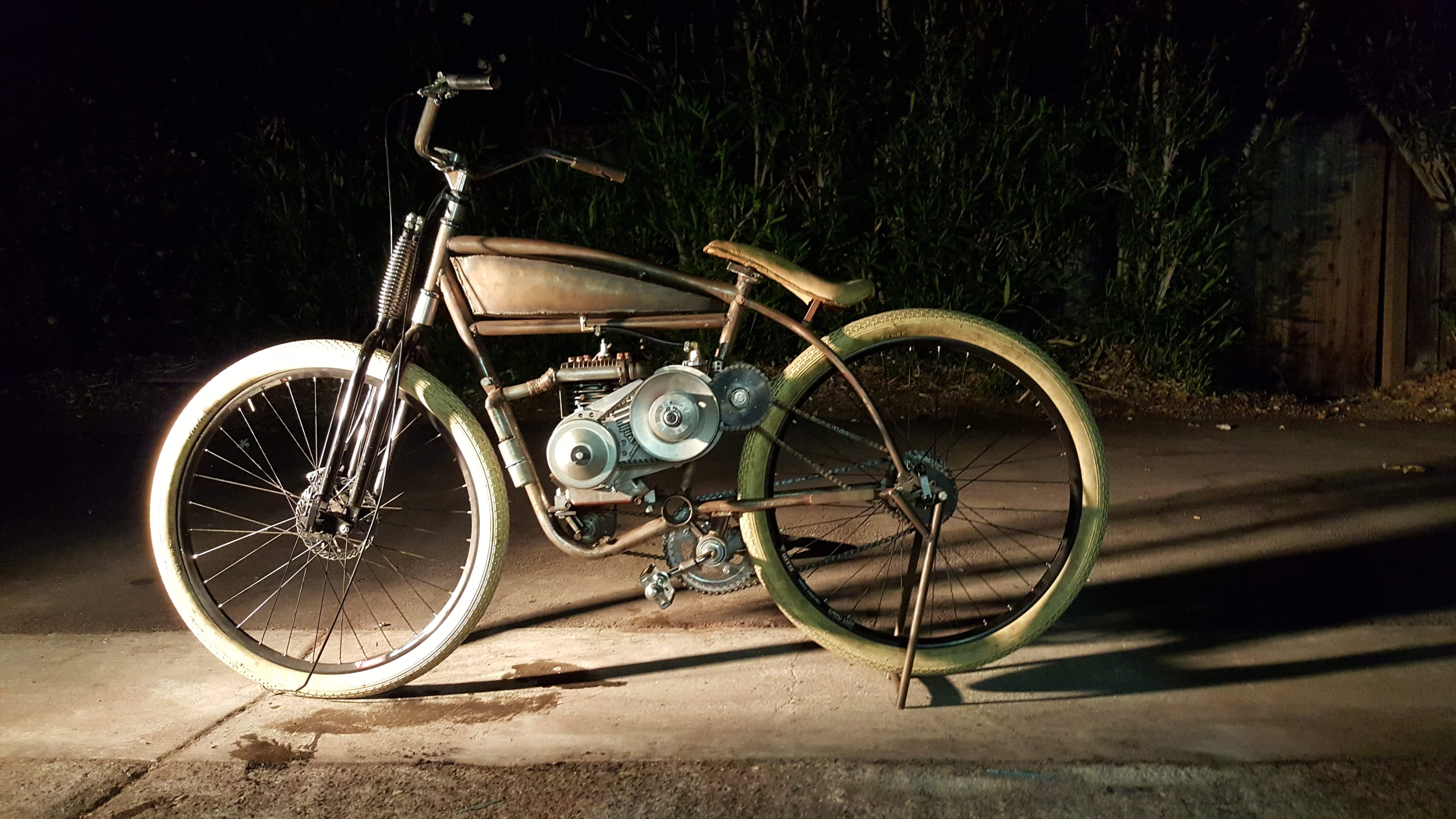
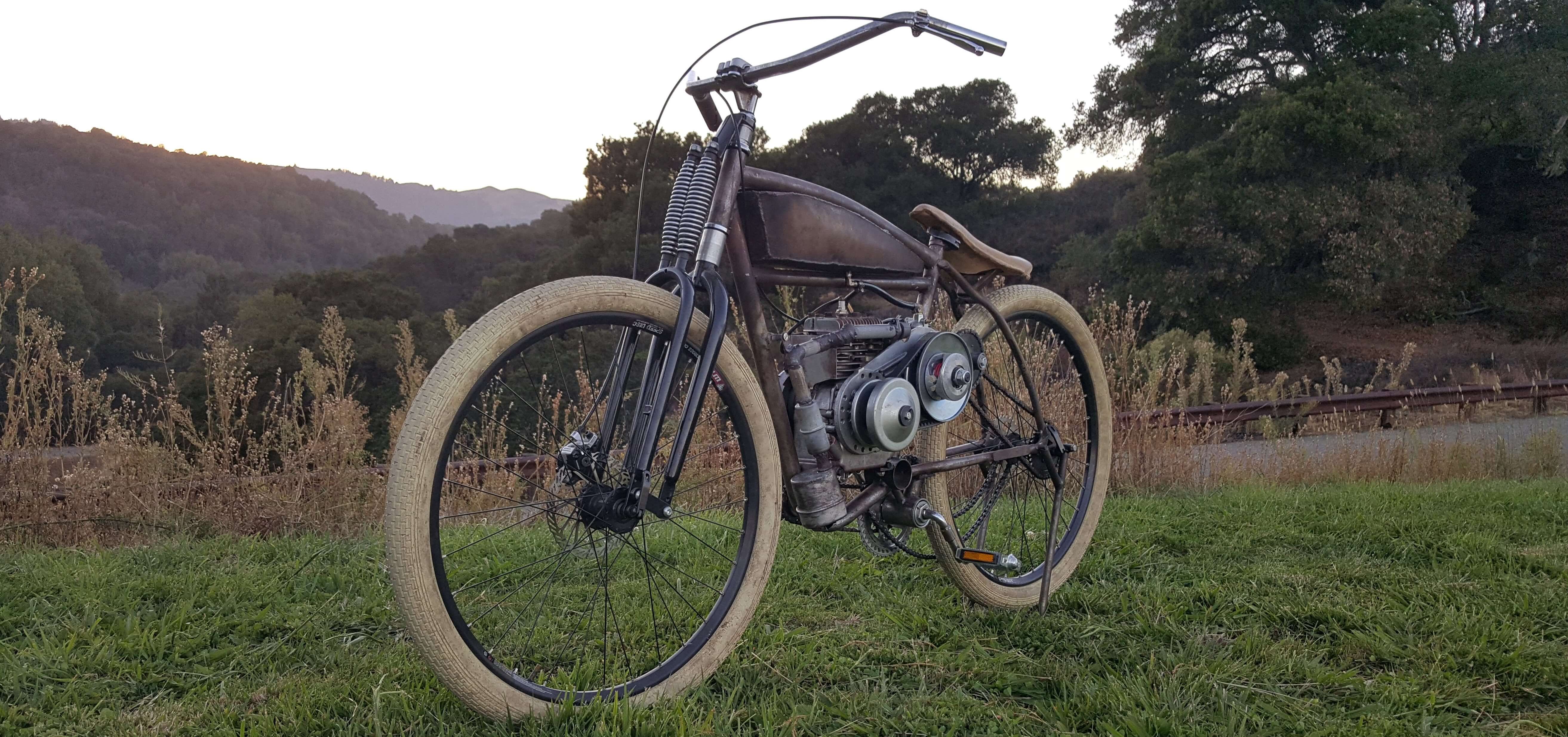